Method for preparing ardealite filler for producing PVC (PVC) material
A PVC material, phosphogypsum technology, applied in the directions of fibrous fillers, chemical instruments and methods, inorganic pigment treatment, etc., can solve the adverse effects of filler processing performance products application performance, affect the PVC and phosphogypsum cross-linked interface stability, Increase the cost of comprehensive utilization of phosphogypsum and other issues, and achieve the effect of being beneficial to optical properties, saving the amount of processing raw materials, and having good flow properties
- Summary
- Abstract
- Description
- Claims
- Application Information
AI Technical Summary
Benefits of technology
Problems solved by technology
Method used
Examples
Embodiment 1
[0020] A preparation method for a phosphogypsum filler used in the production of PVC materials: after mixing 500g of phosphogypsum with 750g of water to obtain a phosphogypsum slurry, adding an alkaline calcium-increasing solution accounting for 2.7% of the mass of the phosphogypsum, soaking for 1 hour, Heating at 180°C for 23 minutes, then adding hydroxypropyl methylcellulose to adjust the pH of the material to 7.0, heating in microwave at 50°C for 3 minutes, sending it into a layered filter for stirring, standing still, and removing the upper layer liquid, drying the material in the lower layer to obtain phosphogypsum filler.
[0021] The pH of the alkaline calcium-increasing liquid is 11.
[0022] The alkaline calcium-increasing liquid is formed by mixing sugar slag and calcium hydroxide in a mass ratio of 1:3.
Embodiment 2
[0024] A preparation method for phosphogypsum filler used in the production of PVC materials: mix 500g of phosphogypsum with 500g of water to obtain a phosphogypsum slurry, add an alkaline calcium-increasing solution accounting for 3% of the mass of phosphogypsum, and soak for 1.3 hours , heated at a temperature of 150°C for 30 minutes, then added hydroxypropyl methylcellulose to adjust the pH of the material to 7.3, heated with microwaves at a temperature of 100°C for 5 minutes, and sent it to a layered filter for stirring and standing still to remove The upper layer is liquid, and the material in the lower layer is dried to obtain phosphogypsum filler.
[0025] The pH of the alkaline calcium-increasing liquid is 10.
[0026] The alkaline calcium-increasing liquid is formed by mixing industrial waste and calcium hydroxide at a mass ratio of 1:2.
[0027] The industrial waste is composed of 30% calcium carbide slag, 35% sugar slag and 35% papermaking black liquor according to th
Embodiment 3
[0029] A preparation method for phosphogypsum filler used in the production of PVC materials: mix 400g of phosphogypsum with 800g of water to obtain a phosphogypsum slurry, add an alkaline calcium-increasing liquid accounting for 2.5% of the mass of phosphogypsum, and soak for 1.5 hours , heated at 200°C for 30 minutes, then added hydroxypropyl methylcellulose to adjust the pH of the material to 7.6, heated with microwaves at a temperature of 78°C for 4 minutes, sent it to a layered filter for stirring, and after standing still, removed The upper layer is liquid, and the material in the lower layer is dried to obtain phosphogypsum filler.
[0030] The pH of the alkaline calcium-increasing liquid is 8.
[0031] The alkaline calcium-increasing liquid is formed by mixing industrial waste and calcium hydroxide in a mass ratio of 1:1.
[0032] The industrial waste is composed of 50% carbide slag and 50% papermaking black liquor according to the mass fraction ratio.
PUM
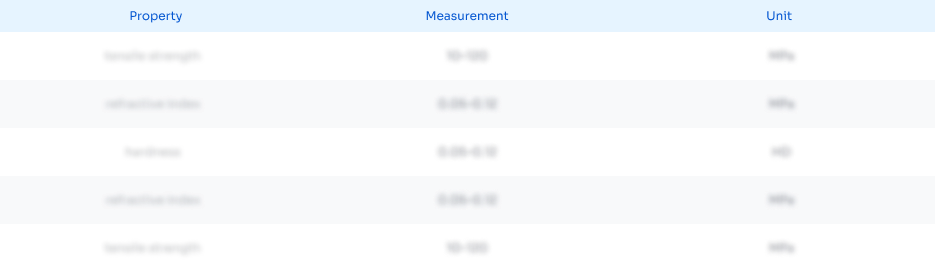
Abstract
Description
Claims
Application Information
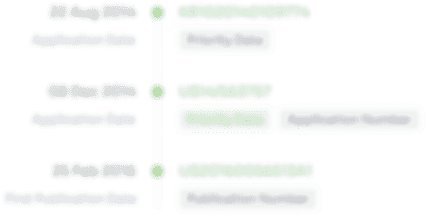
- R&D Engineer
- R&D Manager
- IP Professional
- Industry Leading Data Capabilities
- Powerful AI technology
- Patent DNA Extraction
Browse by: Latest US Patents, China's latest patents, Technical Efficacy Thesaurus, Application Domain, Technology Topic.
© 2024 PatSnap. All rights reserved.Legal|Privacy policy|Modern Slavery Act Transparency Statement|Sitemap