Light flame-retardant fiber plate sandwiched phenolic foam composite plate and manufacturing method thereof
A technology of phenolic foam and production method, which is applied in the direction of chemical instruments and methods, synthetic resin layered products, lamination, etc., can solve the problems of difficult automatic production, low production efficiency, unstable quality, etc., and achieve high production efficiency and manufacturing Low cost, high quality and stable effect
- Summary
- Abstract
- Description
- Claims
- Application Information
AI Technical Summary
Problems solved by technology
Method used
Examples
Example Embodiment
[0027] The specific embodiments of the present invention will be further described below in conjunction with the accompanying drawings.
[0028] figure 1 This is a schematic structural diagram of an embodiment of the present invention. The light flame-retardant fiberboard sandwich phenolic foam composite panel 1 is square, and the reinforced adhesive layer in the light flame-retardant fiberboard sandwich phenolic foam composite panel of the present invention is phenolic resin or amino Any one or two or three kinds of resins or isocyanates are mixed in any ratio of 75-80 parts, curing agent is 1-5 parts, flour is 15.0-25.0 parts, and the components are mixed uniformly according to the weight ratio before use.
[0029] The application method of the enhanced adhesive described in the present application is to apply glue and measure on the surface of the flame-retardant fiberboard or phenolic foam board manually or with a glue spreader.
[0030] figure 2 It is a schematic structural diagr
PUM
Property | Measurement | Unit |
---|---|---|
Thickness | aaaaa | aaaaa |
Thickness | aaaaa | aaaaa |
Abstract
Description
Claims
Application Information
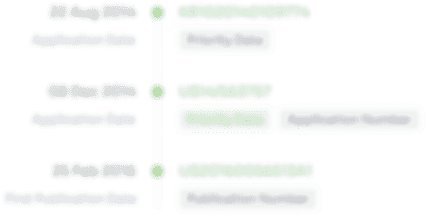
- R&D Engineer
- R&D Manager
- IP Professional
- Industry Leading Data Capabilities
- Powerful AI technology
- Patent DNA Extraction
Browse by: Latest US Patents, China's latest patents, Technical Efficacy Thesaurus, Application Domain, Technology Topic.
© 2024 PatSnap. All rights reserved.Legal|Privacy policy|Modern Slavery Act Transparency Statement|Sitemap