Insulated fireproof coating for optical cables
A technology of insulating fire protection and coating, applied in the direction of fire retardant coatings, coatings, epoxy resin coatings, etc., can solve the problems of short flame retardant time, poor insulation performance, low flame retardant performance, etc., to achieve fast drying, protection and safety, The effect of good fire resistance
- Summary
- Abstract
- Description
- Claims
- Application Information
AI Technical Summary
Benefits of technology
Problems solved by technology
Method used
Examples
Embodiment 1
[0014] An insulating fireproof coating for an optical cable, the raw materials in parts by weight include: 50 parts of 200# solvent oil, 40 parts of ethylene glycol, 35 parts of silicate, 25 parts of glass powder, 15 parts of calcium carbonate, and 10 parts of polytetrafluoroethylene powder 10 parts of epoxy resin, 10 parts of kaolin, 10 parts of aluminum oxide with a particle size of 200 mm, 8 parts of silicon nitride, 8 parts of antimony trioxide with a particle size of 200 mm, 5 parts of mica powder, silicon carbide 5 parts, 5 parts of maleic anhydride, 4 parts of silicone rubber, 4 parts of vermiculite, 3 parts of titanium dioxide, 3 parts of melamine, 3 parts of pentaerythritol, 2 parts of mineral fiber with a particle size of 1 mm, powdered polyvinyl chloride 2 parts, 1 part of boride, 0.4 parts of leveling agent or defoamer.
Embodiment 2
[0016] An insulating fireproof coating for an optical cable, the raw materials in parts by weight include: 52 parts of 200# solvent oil, 45 parts of ethylene glycol, 38 parts of silicate, 26 parts of glass powder, 16 parts of calcium carbonate, and 12 parts of polytetrafluoroethylene powder 11 parts of epoxy resin, 10.5 parts of kaolin, 10.5 parts of aluminum oxide with a particle size of 210 mm, 9 parts of silicon nitride, 8.5 parts of antimony trioxide with a particle size of 210 mm, 8 parts of mica powder, silicon carbide 6 parts, 5.5 parts of maleic anhydride, 4.5 parts of silicone rubber, 4.5 parts of vermiculite, 3.5 parts of titanium dioxide, 3.5 parts of melamine, 3.5 parts of pentaerythritol, 2.5 parts of mineral fiber with a particle size of 1.2mm, powdered polychloride 2.5 parts of ethylene, 1.5 parts of boride, 0.45 parts of leveling agent or defoamer.
Embodiment 3
[0018] An insulating fireproof coating for an optical cable, the raw materials in parts by weight include: 55 parts of 200# solvent oil, 50 parts of ethylene glycol, 40 parts of silicate, 28 parts of glass powder, 18 parts of calcium carbonate, and 15 parts of polytetrafluoroethylene powder 12 parts of epoxy resin, 11 parts of kaolin, 11 parts of aluminum oxide with a particle size of 220 mm, 10 parts of silicon nitride, 9 parts of antimony trioxide with a particle size of 220 mm, 10 parts of mica powder, silicon carbide 8 parts, 6 parts of maleic anhydride, 5 parts of silicone rubber, 5 parts of vermiculite, 4 parts of titanium dioxide, 4 parts of melamine, 4 parts of pentaerythritol, 3 parts of mineral fiber with a particle size of 1.5mm, powdered polychloride 3 parts of ethylene, 2 parts of boride, 0.5 parts of leveling agent.
PUM
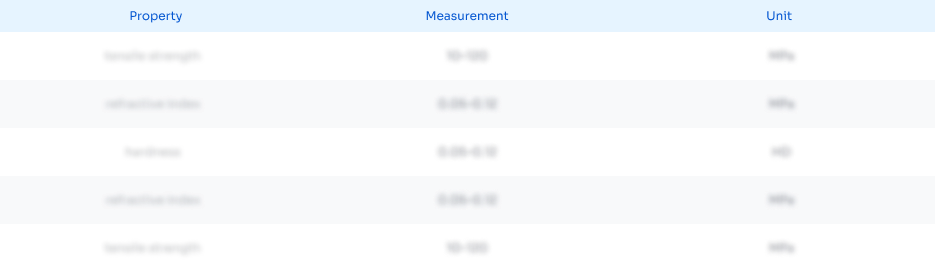
Abstract
Description
Claims
Application Information
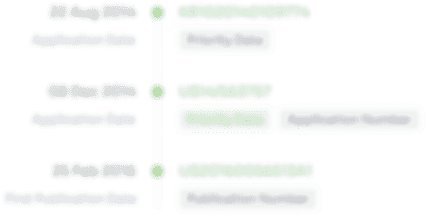
- R&D Engineer
- R&D Manager
- IP Professional
- Industry Leading Data Capabilities
- Powerful AI technology
- Patent DNA Extraction
Browse by: Latest US Patents, China's latest patents, Technical Efficacy Thesaurus, Application Domain, Technology Topic.
© 2024 PatSnap. All rights reserved.Legal|Privacy policy|Modern Slavery Act Transparency Statement|Sitemap