Axial piston machine
An axial piston engine and piston technology, which is used in reciprocating piston engines, mechanical equipment, variable capacity engines, etc., can solve the problems of unfavorable deformation and wear at the bottom of the bearing, and achieve the effect of simple manufacturing.
- Summary
- Abstract
- Description
- Claims
- Application Information
AI Technical Summary
Benefits of technology
Problems solved by technology
Method used
Image
Examples
Embodiment Construction
[0021] figure 1 A longitudinal section through an axial piston machine 100 is shown with a housing 10 consisting of a first housing part 10a and a second housing part 10b. The two housing parts 10 a and 10 b are screwed together by screws 19 .
[0022] In the housing 10, the drive shaft 20 is rotatably supported via two bearings:
[0023] - a first bearing 21, which is configured as a tapered roller bearing and is arranged in the first housing part 10a and
[0024] - A second bearing 22 , which is designed as a plain bearing and is arranged in the second housing part 10 b.
[0025] The second bearing 22 is arranged on the shaft end 25 of the transmission shaft 20 and cooperates with a bearing surface 25 a of the shaft end 25 .
[0026] The first securing ring 26 fixes the inner ring of the first bearing 21 configured as a tapered roller bearing relative to the shoulder of the transmission shaft 20 .
[0027] A second bearing 22 configured as a slide bearing is pressed into th
PUM
Property | Measurement | Unit |
---|---|---|
Convexity | aaaaa | aaaaa |
Abstract
Description
Claims
Application Information
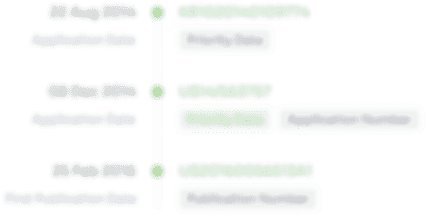
- R&D Engineer
- R&D Manager
- IP Professional
- Industry Leading Data Capabilities
- Powerful AI technology
- Patent DNA Extraction
Browse by: Latest US Patents, China's latest patents, Technical Efficacy Thesaurus, Application Domain, Technology Topic.
© 2024 PatSnap. All rights reserved.Legal|Privacy policy|Modern Slavery Act Transparency Statement|Sitemap