Preparation method of self-support ultrathin diamond single-crystal particles
A diamond single crystal and diamond particle technology, applied in the field of diamond manufacturing, can solve the problems of difficult recycling of chemical etching solution, limitation of particle growth uniformity, inability to achieve low-carbon environmental protection, etc. Achieve dynamic growth and improve uniformity
- Summary
- Abstract
- Description
- Claims
- Application Information
AI Technical Summary
Problems solved by technology
Method used
Examples
Example Embodiment
[0031] Example 1
[0032] In this example, a high-grade CVD diamond powder with an average size of 1.0 μm was prepared.
[0033] First, the surface of the single crystal copper substrate is uniformly ground for 0.5 min by using the mechanical crushing diamond powder, and then the single crystal copper substrate is ultrasonically cleaned in deionized water and acetone solution for 3 to 5 minutes.
[0034] Next, several pre-processed rectangular single crystal copper substrates 2 are placed on the ceramic base 1 deposition table with an interval of 8mm. The hot wire 3 is a twisted pair tantalum wire with a diameter of Φ0.3mm. The heating wires are arranged in parallel at a position 2mm above the single crystal copper substrate at an equal interval of 8mm (such as figure 1 with 2 As shown), the high-temperature-resistant spring is clamped on both ends of each hot wire, so that the hot wire always maintains a straight and horizontal state during the deposition process (the prior art will n
Example Embodiment
[0036] Example 2
[0037] In this example, a high-grade CVD diamond powder with an average size of 5.0 μm was prepared.
[0038] First, the surface of the single crystal copper substrate is uniformly ground for 0.5 min by using the mechanical crushing diamond powder, and then the single crystal copper substrate is ultrasonically cleaned in deionized water and acetone solution for 3 to 5 minutes.
[0039] Next, place several pretreated rectangular single crystal copper substrates on the ceramic base deposition table with a pitch of 10mm. The heating wire is a twisted pair tantalum wire with a diameter of Φ0.4mm, and then a few heating wires Arranged in parallel with an equal spacing of 10mm at a position 3mm above the single crystal copper substrate (e.g. figure 1 with 2 As shown), the high temperature resistant spring is clamped on both ends of each hot wire, so that the hot wire always maintains a straight and horizontal state during the deposition process. After the reaction chamber
Example Embodiment
[0041] Example 3
[0042] In this example, a high-grade CVD diamond powder with an average size of 10.0 μm was prepared.
[0043] First, the surface of the single crystal copper substrate is uniformly ground for 0.5 min by using the mechanical crushing diamond powder, and then the single crystal copper substrate is ultrasonically cleaned in deionized water and acetone solution for 3 to 5 minutes.
[0044] Next, several pre-processed rectangular single crystal copper substrates are placed on the ceramic base deposition table with a spacing of 8mm (such as figure 1 As shown), the heating wire adopts a twisted pair tantalum wire with a diameter of Φ0.4mm, and then several heating wires are arranged in parallel at a position 3mm above the single crystal copper substrate at an equal interval of 8mm (such as figure 2 As shown), the high temperature resistant spring is clamped on both ends of each hot wire, so that the hot wire always maintains a straight and horizontal state during the depos
PUM
Property | Measurement | Unit |
---|---|---|
Average size | aaaaa | aaaaa |
Average size | aaaaa | aaaaa |
Average size | aaaaa | aaaaa |
Abstract
Description
Claims
Application Information
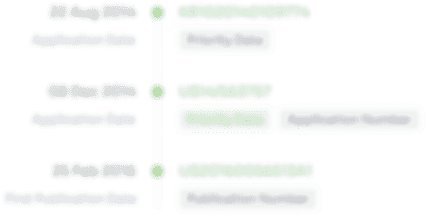
- R&D Engineer
- R&D Manager
- IP Professional
- Industry Leading Data Capabilities
- Powerful AI technology
- Patent DNA Extraction
Browse by: Latest US Patents, China's latest patents, Technical Efficacy Thesaurus, Application Domain, Technology Topic.
© 2024 PatSnap. All rights reserved.Legal|Privacy policy|Modern Slavery Act Transparency Statement|Sitemap