Method for preparing wollastonite toughened epoxy resin
A technology of tough epoxy resin and epoxy resin, which is applied in the field of preparation of wollastonite toughened epoxy resin, can solve the problems of product mechanical property decline, limitation of wollastonite application, uneven dispersion, etc., to improve performance and tensile strength and impact strength improvement, dispersibility and stability improvement effect
- Summary
- Abstract
- Description
- Claims
- Application Information
AI Technical Summary
Benefits of technology
Problems solved by technology
Method used
Examples
Embodiment 1
[0019] A kind of preparation method of wollastonite toughened epoxy resin described in the present embodiment 1, comprises the following steps:
[0020] (1) Hydrolyze the silane coupling agent KH-570 in a mixed solution of absolute ethanol and deionized water for 1.5h, add it to a round bottom flask, and add a certain amount of wollastonite; the volume ratio of ethanol to water is 1 : 1, the consumption of coupling agent is 1-30% of wollastonite quality;
[0021] (2) Put the flask in 50°C waters, react under electromagnetic stirring for 2.5h, after the reaction, the mixed solution is suction filtered, and the sediment is placed in a vacuum oven and dried at 110°C for 11 h;
[0022] (3) Grinding the dry modified wollastonite in a planetary ball mill for 1.5 h at a stirring rate of 200-1000r / min to obtain wet-process modified wollastonite;
[0023] (4) The modified wollastonite is mixed with bisphenol A epoxy resin 127 and ground for 3 hours by a three-roll mill to obtain a mast
Embodiment 2
[0028] A kind of preparation method of wollastonite toughened epoxy resin described in present embodiment 2, comprises the following steps:
[0029] (1) Hydrolyze the silane coupling agent KH-570 in a mixed solution of absolute ethanol and deionized water for 2 hours, add it into a round bottom flask, and add a certain amount of wollastonite; the volume ratio of ethanol to water is 1: 4. The amount of coupling agent is 1-30% of the wollastonite mass;
[0030] (2) Put the flask in 80°C waters, and react for 3h under electromagnetic stirring. After the reaction, the mixed solution is suction-filtered, and the sediment is placed in a vacuum oven and dried at 120°C for 12h;
[0031] (3) Grinding the dry modified wollastonite in a planetary ball mill for 2 hours at a stirring rate of 200-1000r / min to obtain wet-process modified wollastonite;
[0032] (4) The modified wollastonite is mixed with bisphenol A epoxy resin 127 and ground for 3 hours by a three-roll mill to obtain a maste
Embodiment 3
[0037] A kind of preparation method of wollastonite toughened epoxy resin described in present embodiment 3, comprises the following steps:
[0038] (1) Hydrolyze the silane coupling agent KH-570 in a mixed solution of absolute ethanol and deionized water for 2 hours, add it into a round bottom flask, and add a certain amount of wollastonite; the volume ratio of ethanol to water is 1: 5. The amount of coupling agent is 1-30% of the wollastonite mass;
[0039] (2) Put the flask in water at 85°C and react for 3h under electromagnetic stirring. After the reaction is over, filter the mixture with suction, and place the sediment in a vacuum oven to dry at 130°C for 13h;
[0040] (3) Grinding the dry modified wollastonite in a planetary ball mill for 2 hours at a stirring rate of 200-1000r / min to obtain wet-process modified wollastonite;
[0041] (4) The modified wollastonite is mixed with bisphenol A epoxy resin 127 and ground for 3 hours by a three-roll mill to obtain a masterbatc
PUM
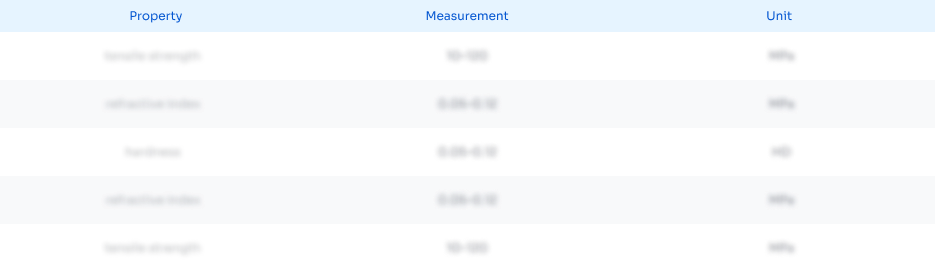
Abstract
Description
Claims
Application Information
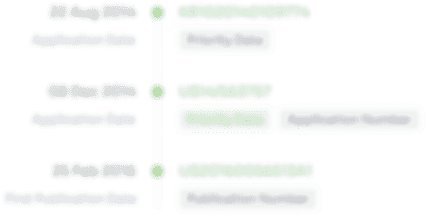
- R&D Engineer
- R&D Manager
- IP Professional
- Industry Leading Data Capabilities
- Powerful AI technology
- Patent DNA Extraction
Browse by: Latest US Patents, China's latest patents, Technical Efficacy Thesaurus, Application Domain, Technology Topic.
© 2024 PatSnap. All rights reserved.Legal|Privacy policy|Modern Slavery Act Transparency Statement|Sitemap