Special HIPS panel toughening color masterbatch for refrigerator, preparation method and application thereof
- Summary
- Abstract
- Description
- Claims
- Application Information
AI Technical Summary
Problems solved by technology
Method used
Image
Examples
Example Embodiment
[0028] An embodiment of another aspect of the present invention provides a method for preparing a HIPS sheet toughening color masterbatch for refrigerators as described in any of the above technical solutions, comprising the following steps:
[0029] Compounding and stirring process: Accurately weigh the main material, styrene-butadiene-styrene block copolymer toughening agent, white oil, titanium dioxide, pigment and dispersant according to the parts by weight, and add styrene according to the first -Butadiene-styrene block copolymer toughening agent, then adding white oil, and finally adding the main ingredient, titanium dioxide, pigment and dispersant in the order of adding the above components and stirring evenly to obtain a compounded material;
[0030] Pelletizing process: The compounded material is fed into a twin-screw underwater pelletizer with a preset temperature and extruded into a pelletizer. The compounded material is melted at high temperature, and then blended by t
Example Embodiment
[0037] Example 1
[0038] Accurately weigh 28 parts of HIPS 825, 30 parts of SBS, 10 parts of white oil, 28 parts of rutile titanium dioxide, 0.5 part of pigment, 1 part of BASF A wax and 2.5 parts of ethylene bis-stearic acid amide according to parts by weight, After adding SBS and white oil successively, start stirring for 1-2 minutes, then stop and stand for 3-4 minutes, then add HIPS 825, rutile titanium dioxide, pigment, BASF A wax and ethylene bis-stearic acid amide in sequence The above components are evenly stirred to obtain compounding materials;
[0039] The compounded material is fed into the twin-screw underwater pelletizer extrusion granulator, and the compounded material sequentially passes through the feeding section at 150 °C-170 °C, the melting section at 170 °C-180 °C, and the plasticizing section at 180 °C-195 °C. After the head zone is melted at a high temperature of 200°C, it undergoes twin-screw high-speed shearing and blending, extrusion, underwater dicing
Example Embodiment
[0040] Example 2
[0041] Accurately weigh 26 parts of HIPS 825, 31 parts of SBS, 11 parts of white oil, 28 parts of rutile type titanium dioxide, 0.5 parts of pigment, 1 part of BASF A wax and 2.5 parts of ethylene bis-stearic acid amide according to parts by weight, and according to the After adding SBS and white oil successively, start stirring for 1-2 minutes, then stop and stand for 3-4 minutes, then add HIPS 825, rutile titanium dioxide, pigment, BASF A wax and ethylene bis-stearic acid amide in sequence The above components are evenly stirred to obtain compounding materials;
[0042] The compounded material is fed into the twin-screw underwater pelletizer extrusion granulator, and the compounded material sequentially passes through the feeding section at 150 °C-170 °C, the melting section at 170 °C-180 °C, and the plasticizing section at 180 °C-195 °C. After melting at a high temperature of 200°C in the head zone, through twin-screw high-speed shearing and blending, extru
PUM
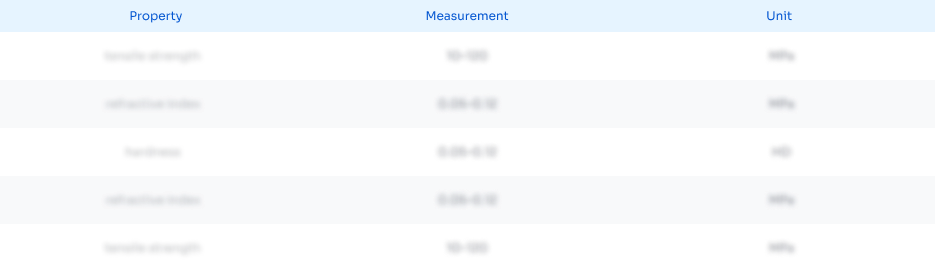
Abstract
Description
Claims
Application Information
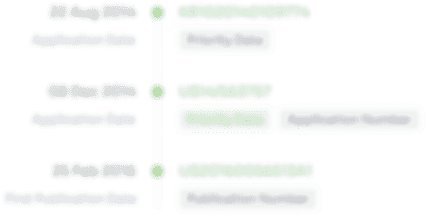
- R&D Engineer
- R&D Manager
- IP Professional
- Industry Leading Data Capabilities
- Powerful AI technology
- Patent DNA Extraction
Browse by: Latest US Patents, China's latest patents, Technical Efficacy Thesaurus, Application Domain, Technology Topic.
© 2024 PatSnap. All rights reserved.Legal|Privacy policy|Modern Slavery Act Transparency Statement|Sitemap