Preparation of the high-performance porcelain heating parts with automatic temperature-control
A ceramic heating, high-performance technology, used in heating elements, heating element materials, ohmic resistance heating components, etc., can solve the problems of inability to perform automatic temperature control, limited application occasions, short service life, etc., and achieve a high qualified rate of finished products. , Environmental pollution-free, low production costs
- Summary
- Abstract
- Description
- Claims
- Application Information
AI Technical Summary
Problems solved by technology
Method used
Image
Examples
example 1
[0010] Example 1, as shown in Figures 1 and 2, its formula is 66% of high-purity, ultra-fine aluminum nitride powder with an average particle size of less than 0.5 microns, an oxygen content of less than 0.84%, and an aluminum nitride content greater than 99%, adding 25% nano-nitrogen Aluminum powder and additive 5% YF 3 , 4% CaF 2 ; After 60 hours of ball milling the raw material nitrogen protection cylinder, the mill was passed through a 60-mesh sieve, wherein the material of the ball mill tank was polyurethane, and the grinding balls were zirconia balls, material: ball = 1: 3, and 0.2% oleic acid was added before ball milling; sieve Add 0.35% PVA and 0.25% emulsified paraffin to the material, mix and granulate under nitrogen protection; 220-250 Mf high pressure molding and insert heating resistance molybdenum wire (4) in the middle of the powder, keep warm at 1880°C for 6 hours under high temperature flowing nitrogen atmosphere protection Sintered into an electric heating ...
example 2
[0011] Example two, as shown in Figures 1 and 2, its formula is 76.2% of high-purity, ultra-fine aluminum nitride powder with an average particle size of less than 0.5 microns, an oxygen content of less than 0.84%, and an aluminum nitride content greater than 99%, adding 20% nano-nitrogen Aluminum powder and additive 3.8% Y 2 o 3 ; After 60 hours of ball milling the raw material nitrogen protection cylinder, the mill was passed through a 60-mesh sieve, wherein the material of the ball mill tank was polyurethane, and the grinding balls were zirconia balls, material: ball = 1: 3, and 0.2% oleic acid was added before ball milling; sieve Add 0.30% PVA and 0.20% emulsified paraffin to the material, mix and granulate under nitrogen protection; 220-250 Mf high pressure molding and insert heating resistance tungsten wire (4) in the middle of the powder, keep warm at 1850°C for 4.5 hours under high temperature flowing nitrogen atmosphere protection Hot pressing and sintering into an...
example 3
[0012] Example three, as shown in Figures 1 and 2, its formula is 70% of high-purity, ultra-fine aluminum nitride powder with an average particle size less than 0.5 micron, oxygen content less than 0.84%, and aluminum nitride content greater than 99%, adding 25% nano-nitrogen Aluminum powder and additive 3% Y 2 o 3 , 2% CaF 2 ; After 60 hours of ball milling the raw material nitrogen protection cylinder, the mill was passed through a 60-mesh sieve, wherein the material of the ball mill tank was polyurethane, and the grinding balls were zirconia balls, material: ball = 1: 3, and 0.2% oleic acid was added before ball milling; sieve Add 0.30% PVA and 0.20% emulsified paraffin to the material, mix and granulate under nitrogen protection; 220-250 Mf high pressure molding and insert heating resistance molybdenum wire (4) in the middle of the powder, keep warm at 1850 ° C for 6 hours and protect under high temperature flowing nitrogen atmosphere Hot pressing and sintering into an e...
PUM
Property | Measurement | Unit |
---|---|---|
particle size | aaaaa | aaaaa |
Abstract
Description
Claims
Application Information
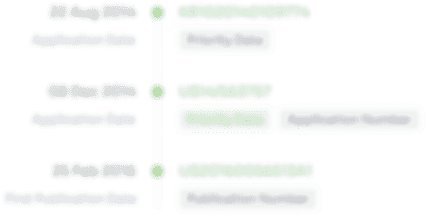
- R&D Engineer
- R&D Manager
- IP Professional
- Industry Leading Data Capabilities
- Powerful AI technology
- Patent DNA Extraction
Browse by: Latest US Patents, China's latest patents, Technical Efficacy Thesaurus, Application Domain, Technology Topic.
© 2024 PatSnap. All rights reserved.Legal|Privacy policy|Modern Slavery Act Transparency Statement|Sitemap