Production method of large-wall-thickness straight-seam submerged-arc-welded pipeline steel plate
A technology of straight seam submerged arc welding and production methods, which is applied in the field of pipeline steel plates, can solve the problems of pipe manufacturers and base metal production plants, the roundness of steel pipes exceeds the standard requirements, and affects the production rhythm of steel pipe factories, etc., and achieves the same plate mechanics The effects of high performance uniformity, small grain size variance, and small roundness deviation
- Summary
- Abstract
- Description
- Claims
- Application Information
AI Technical Summary
Benefits of technology
Problems solved by technology
Method used
Image
Examples
Embodiment 1
[0062] Embodiment 1: The production method of the large wall thickness longitudinal submerged arc welding pipeline steel plate adopts the following specific process.
[0063] (1) Steelmaking-continuous casting process: the weight percentage of casting slab composition is: C: 0.03%, Si: 0.045%, Mn: 1.7%, P: 0.014%, S: 0.0016%, Als: 0.015%, Cr: 0.30%, Nb: 0.070%, Ti: 0.030%, and the balance is Fe and unavoidable impurities.
[0064] (2) Heating process: the temperature of the heating section is 1190°C, the temperature of the soaking section is 1140°C, the temperature of the soaking section is kept for 90 minutes, and the difference between the temperature of the heating section and the temperature of the soaking section is 50°C.
[0065] (3) Rolling process: TMCP double-pass rolling process is adopted; in the first rolling pass, the starting temperature is 1120°C, the temperature at the end pass is 1040°C, and the reduction rate at the end pass is 25.0%; The rolling temperature ra
Embodiment 2
[0070] Embodiment 2: The production method of the large wall thickness longitudinal submerged arc welding pipeline steel plate adopts the following specific process.
[0071] (1) Steelmaking-continuous casting process: the weight percentage of casting slab composition is: C: 0.04%, Si: 0.038%, Mn: 1.62%, P: 0.010%, S: 0.0010%, Als: 0.031%, Cr: 0.28%, Nb: 0.067%; Ti: 0.027%, the balance is Fe and unavoidable impurities.
[0072] (2) Heating process: the temperature of the heating section is 1182°C, the temperature of the soaking section is 1130°C, the temperature of the soaking section is kept for 76 minutes, and the difference between the temperature of the heating section and the temperature of the soaking section is 52°C.
[0073] (3) Rolling process: TMCP double-pass rolling process is adopted; in the first rolling pass, the starting temperature is 1112°C, the temperature at the end pass is 1031°C, and the reduction rate at the end pass is 26.3%; The rolling temperature range
Embodiment 3
[0078] Embodiment 3: The production method of the large wall thickness longitudinal submerged arc welding pipeline steel plate adopts the following specific process.
[0079] (1) Steelmaking-continuous casting process: the weight percentage of casting slab composition is: C: 0.05%, Si: 0.029%, Mn: 1.6%, P: 0.012%, S: 0.0008%, Als: 0.037%, Cr: 0.25%, Nb: 0.064%; Ti: 0.025%, the balance is Fe and unavoidable impurities.
[0080] (2) Heating process: the temperature of the heating section is 1168°C, the temperature of the soaking section is 1125°C, the temperature of the soaking section is 64 minutes, and the difference between the temperature of the heating section and the temperature of the soaking section is 43°C.
[0081] (3) Rolling process: TMCP dual-pass rolling process is adopted; in the first rolling pass, the starting temperature is 1110°C, the temperature at the end pass is 1025°C, and the reduction rate at the end pass is 27.5%; The rolling temperature is 925°C, and the
PUM
Property | Measurement | Unit |
---|---|---|
Yield strength | aaaaa | aaaaa |
Tensile strength | aaaaa | aaaaa |
Yield strength | aaaaa | aaaaa |
Abstract
Description
Claims
Application Information
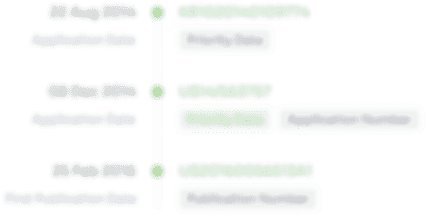
- R&D Engineer
- R&D Manager
- IP Professional
- Industry Leading Data Capabilities
- Powerful AI technology
- Patent DNA Extraction
Browse by: Latest US Patents, China's latest patents, Technical Efficacy Thesaurus, Application Domain, Technology Topic.
© 2024 PatSnap. All rights reserved.Legal|Privacy policy|Modern Slavery Act Transparency Statement|Sitemap