Preparation method of large-sized compact silicon carbide ceramic plate
A large-scale technology of silicon carbide ceramics, applied in the field of silicon carbide ceramics, can solve the problems of easy cracking, uneven density, poor compactness, etc., and achieve the effects of improving production efficiency, ensuring sintering quality, and increasing density
- Summary
- Abstract
- Description
- Claims
- Application Information
AI Technical Summary
Problems solved by technology
Method used
Image
Examples
Embodiment 1
[0022] Prepare a silicon carbide ceramic plate with a length×width×thickness of 600mm×400mm×40mm by the following method, including the following steps:
[0023] 1) Mixing mix 1 part by weight of graphite powder with a purity of 99.8 to 99.9% and 25 parts by weight of silicon carbide powder with a purity of 99.8 to 99.9%, and then add 2 parts by weight of zinc stearate and 15 parts by weight of The polyvinyl alcohol is uniformly stirred to obtain a mixture;
[0024] 2) Spray granulation adopts a centrifugal spray dryer to spray and granulate the mixture to obtain granulated powder;
[0025] 3) Hot-press forming Put the prepared granulated powder into a metal mold, use a 500-600T hot-press machine, pressurize and release pressure 4 times under the conditions of temperature 180°C and pressure 35MPa, and obtain a hot-press forming plate body;
[0026] 4) Humidification and drying Place the formed green body in a humidification and drying equipment, and slowly humidify and dry for
Embodiment 2
[0031] Prepare a silicon carbide ceramic plate with a length×width×thickness of 700mm×500mm×50mm by the following method, including the following steps:
[0032] 1) Mixing mix 1.4 parts by weight of graphite powder with a purity of 99.8 to 99.9% and 28 parts by weight of silicon carbide powder with a purity of 99.8 to 99.9%, and then add 3 parts by weight of zinc stearate and 18 parts by weight of The polyvinyl alcohol is uniformly stirred to obtain a mixture;
[0033] 2) Spray granulation adopts a centrifugal spray dryer to spray and granulate the mixture to obtain granulated powder;
[0034] 3) Hot-press forming Put the prepared granulated powder into a metal mold, use a 500-600T hot-press machine, pressurize and release the pressure 5 times at a temperature of 190°C and a pressure of 45MPa, and obtain a hot-press-formed plate body;
[0035] 4) Humidification and drying Place the formed green body in a humidification and drying equipment, and slowly humidify and dry for 110 h
Embodiment 3
[0040] Prepare a silicon carbide ceramic plate with a length×width×thickness of 800mm×600mm×60mm by the following method, including the following steps:
[0041] 1) Mixing After mixing 2 parts by weight of graphite powder with a purity of 99.8 to 99.9% and 30 parts by weight of silicon carbide powder with a purity of 99.8 to 99.9%, add 4 parts by weight of zinc stearate and 20 parts by weight of The polyvinyl alcohol is uniformly stirred to obtain a mixture;
[0042] 2) Spray granulation adopts a centrifugal spray dryer to spray and granulate the mixture to obtain granulated powder;
[0043]3) Hot-press forming Put the prepared granulated powder into a metal mold, use a 500-600T hot press, pressurize and release the pressure under the conditions of a temperature of 200°C and a pressure of 55MPa, and obtain a blank of a hot-pressed forming plate body;
[0044] 4) Humidification and drying Place the formed body in a humidification and drying equipment, and slowly humidify and dry
PUM
Property | Measurement | Unit |
---|---|---|
Thickness | aaaaa | aaaaa |
Abstract
Description
Claims
Application Information
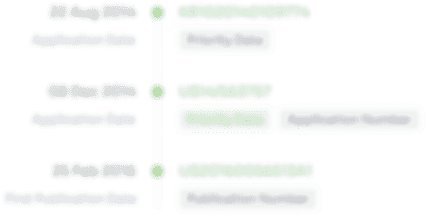
- R&D Engineer
- R&D Manager
- IP Professional
- Industry Leading Data Capabilities
- Powerful AI technology
- Patent DNA Extraction
Browse by: Latest US Patents, China's latest patents, Technical Efficacy Thesaurus, Application Domain, Technology Topic.
© 2024 PatSnap. All rights reserved.Legal|Privacy policy|Modern Slavery Act Transparency Statement|Sitemap