A method for preparing the main carbon strip structure of a pantograph carbon slide plate
A pantograph carbon slide plate and carbon strip technology, which is applied in the direction of current collectors, electric vehicles, power collectors, etc., can solve the problems of poor product quality stability and controllability, uneven metal liquid immersion, easy cracking friction resistance, etc. , to achieve the effects of stable and reliable product quality, convenient processing, and improved crack resistance
- Summary
- Abstract
- Description
- Claims
- Application Information
AI Technical Summary
Benefits of technology
Problems solved by technology
Method used
Image
Examples
specific Embodiment approach
[0030] Specific implementation method: participate in Figure 6 A method for preparing the main carbon strip structure of a pantograph carbon slide, including the steps of mixing carbon powder into asphalt material and pressing to obtain the main carbon strip, and fixing the main carbon strip on the aluminum support by bonding The step is characterized in that after the main carbon strip is formed, it is put into engine oil and boiled, and then kept at 65-85°C for 48-72 hours.
[0031] Like this, through above-mentioned method, can make the upper surface of main carbon bar generate one layer of oil film layer. In this way, the oil film layer can be relied on to better reduce the friction and improve the sliding effect.
[0032] The oil film layer prepared by the above method can make the oil molecules bond and attach around the carbon particles on the surface of the main carbon strip, greatly improving the sliding friction effect of the carbon particles on the surface of the mai
PUM
Property | Measurement | Unit |
---|---|---|
Width | aaaaa | aaaaa |
Abstract
Description
Claims
Application Information
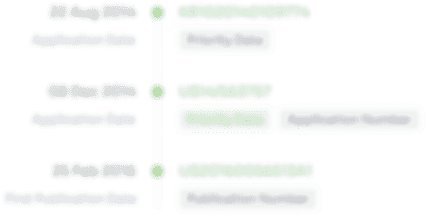
- R&D Engineer
- R&D Manager
- IP Professional
- Industry Leading Data Capabilities
- Powerful AI technology
- Patent DNA Extraction
Browse by: Latest US Patents, China's latest patents, Technical Efficacy Thesaurus, Application Domain, Technology Topic.
© 2024 PatSnap. All rights reserved.Legal|Privacy policy|Modern Slavery Act Transparency Statement|Sitemap