Novel anti-electrostatic ceramic glaze as well as preparation method and application thereof
An anti-static, ceramic glaze technology, applied in the field of ceramics, can solve the problems of deep color, application limitation, unstable performance, etc., and achieve the effect of good chemical stability and low price
- Summary
- Abstract
- Description
- Claims
- Application Information
AI Technical Summary
Benefits of technology
Problems solved by technology
Method used
Examples
Embodiment 1
[0033] Preparation of aluminum-doped zinc oxide conductive powder:
[0034] (1) Combine ZnO and Al 2 o 3 The powder is put into a ball mill jar, where Al 2 o 3 The powder is 2.5% of the total amount of powder, and the weight ratio of powder, balls and ethanol is 1:1.6:1, adding balls and ethanol solution to disperse, milling and mixing on a ball mill, and the ball milling time is 12h;
[0035] (2) Put it into a drying oven after mixing evenly, and dry it at 100°C;
[0036] (3) Put the dried mixed powder into an alumina crucible, place the crucible in a microwave continuous synthesis furnace for synthesis, the microwave power is generally 5kW, the synthesis condition is 1250°C, and the temperature is kept for 1h to obtain the conductive powder;
[0037] (4) Put the conductive powder synthesized by microwave into the ball mill tank, and grind it in the ball mill according to the weight ratio of the conductive powder and the ball at 1:2. The ball milling time is 3 hours. Zinc c
Embodiment 2
[0044] Preparation of aluminum-doped zinc oxide conductive powder:
[0045] (1) Combine ZnO and Al 2 o 3 The powder is put into a ball mill jar, where Al 2 o 3 The powder is 1.25% of the total amount of powder, and then the weight ratio of powder, balls and ethanol is 1:2:0.5, adding balls and ethanol solution to disperse, and performing ball milling on a ball mill for 15 hours;
[0046](2) Put it into a drying oven after mixing evenly, and dry it at 100°C;
[0047] (3) Put the dried mixed powder into an alumina crucible, place the crucible in a microwave continuous synthesis furnace for synthesis, the microwave power is generally selected as 3kW, the synthesis condition is 1300°C, and the temperature is kept for 0.5h to obtain the conductive powder;
[0048] (4) Put the conductive powder synthesized by microwave into the ball mill tank, and grind it in the ball mill according to the weight ratio of the conductive powder and the ball at 1:1.8. The ball milling time is 2 hours
Embodiment 3
[0055] Preparation of aluminum-doped zinc oxide conductive powder:
[0056] (1) Combine ZnO and Al 2 o 3 The powder is put into a ball mill jar, where Al 2 o 3 The powder is 2.0% of the total amount of powder, and then the weight ratio of powder, balls and ethanol is 1:1.8:0.8, adding balls and ethanol solution to disperse, performing ball milling and mixing on a ball mill, and the ball milling time is 10h;
[0057] (2) Put it into a drying oven after mixing evenly, and dry it at 100°C;
[0058] (3) Put the dried mixed powder into an alumina crucible, place the crucible in a microwave continuous synthesis furnace for synthesis, the microwave power is generally selected as 1kW, the synthesis condition is 1200°C, and the temperature is kept for 0.8h to obtain the conductive powder;
[0059] (4) Put the conductive powder synthesized by microwave into the ball mill tank, and grind it in the ball mill according to the weight ratio of the conductive powder and the ball at 1:1.6. Th
PUM
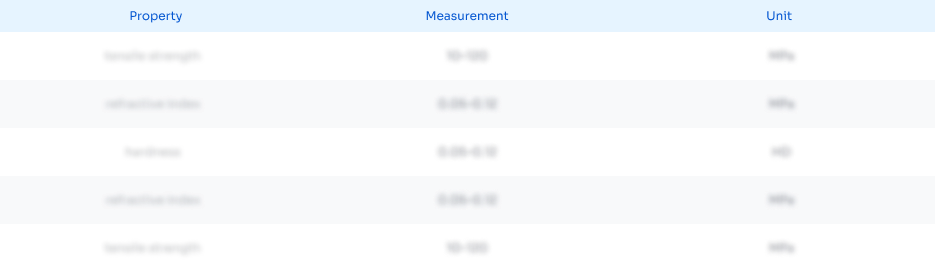
Abstract
Description
Claims
Application Information
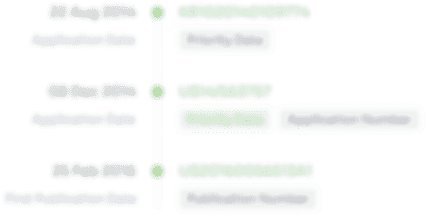
- R&D Engineer
- R&D Manager
- IP Professional
- Industry Leading Data Capabilities
- Powerful AI technology
- Patent DNA Extraction
Browse by: Latest US Patents, China's latest patents, Technical Efficacy Thesaurus, Application Domain, Technology Topic.
© 2024 PatSnap. All rights reserved.Legal|Privacy policy|Modern Slavery Act Transparency Statement|Sitemap