Preparation method of high-temperature-resistant folding-resistant soldering-resistant ink
A technology of solder mask ink and high temperature resistance, applied in the field of solder mask ink preparation, can solve the problems of poor folding resistance, poor heat resistance of solder mask ink, etc., and achieve excellent tensile properties, high temperature resistance, good heat resistance, etc. properties, high tensile properties and high temperature resistance
- Summary
- Abstract
- Description
- Claims
- Application Information
AI Technical Summary
Problems solved by technology
Method used
Image
Examples
Example Embodiment
[0025] Example 1
[0026] Put corn stalks and bagasse of equal quality into an electric furnace to obtain combustion products, put the combustion products in a porcelain crucible, and then put the porcelain crucible in a high-temperature furnace, and raise the temperature of the high-temperature furnace to 580℃ in an argon atmosphere , Calcined at a constant temperature for 4 hours and then ground through a 400-mesh sieve to obtain a calcined product for use; in parts by weight, weigh 40 parts of alicyclic epoxy acrylate monomer, 30 parts of hydroxyethyl methacrylate, and 2 parts of acetone , 2 parts of azobisisobutyronitrile and 0.5 part of 3-mercaptopropionic acid isooctyl ester were mixed and put into a beaker, mixed and stirred at a speed of 300r / min until all dissolved to obtain a mixed solution; put acetone into the reactor, and react Seal the kettle and heat it up to 75℃, and let it stand at constant temperature for 30 minutes. After standing, keep the temperature unchanged
Example Embodiment
[0027] Example 2
[0028] Put corn stalks and bagasse of equal quality in an electric furnace to obtain combustion products, put the combustion products in a porcelain crucible, then put the porcelain crucible in a high-temperature furnace, and raise the temperature of the high-temperature furnace to 590℃ in an argon atmosphere , Calcined at a constant temperature for 4 hours and then ground through a 400-mesh sieve to obtain a calcined product for use; in parts by weight, weigh 43 parts of alicyclic epoxy acrylate monomer, 33 parts of hydroxyethyl methacrylate, and 2 parts of acetone , 2 parts azobisisobutyronitrile and 0.7 parts isooctyl 3-mercaptopropionate were mixed and put into a beaker, mixed and stirred at a speed of 330r / min until all dissolved to obtain a mixed solution; put acetone into the reaction kettle, and react Seal the kettle and heat it up to 77°C, let it stand at constant temperature for 35 minutes, after standing still, keep the temperature unchanged and under
Example Embodiment
[0029] Example 3
[0030] Put corn stalks and bagasse of equal quality into an electric furnace to obtain combustion products, put the combustion products in a porcelain crucible, and then put the porcelain crucible in a high-temperature furnace, and raise the temperature of the high-temperature furnace to 600°C in an argon atmosphere , Calcined at a constant temperature for 5 hours and then ground through a 400-mesh sieve to obtain a calcined product for use; in parts by weight, weigh out 45 parts of alicyclic epoxy acrylate monomer, 35 parts of hydroxyethyl methacrylate, and 3 parts of acetone , 3 parts of azobisisobutyronitrile and 0.8 parts of 3-mercaptopropionate isooctyl ester were mixed and put into a beaker, mixed and stirred at a speed of 360r / min until all dissolved to obtain a mixed solution; put acetone into the reactor, and react Seal the kettle and heat it up to 80℃, and let stand at constant temperature for 40 minutes. After standing, keep the temperature constant a
PUM
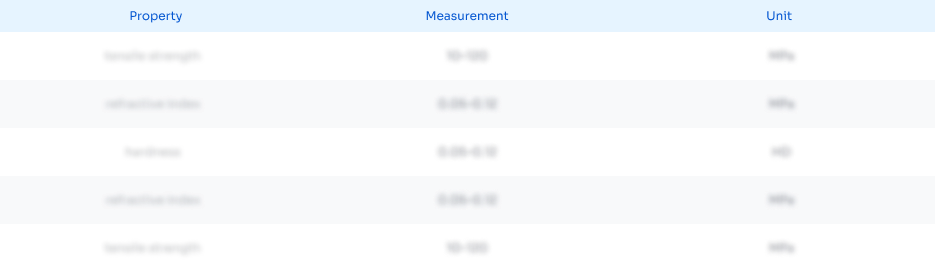
Abstract
Description
Claims
Application Information
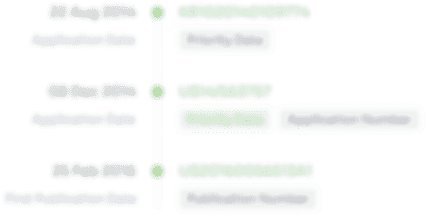
- R&D Engineer
- R&D Manager
- IP Professional
- Industry Leading Data Capabilities
- Powerful AI technology
- Patent DNA Extraction
Browse by: Latest US Patents, China's latest patents, Technical Efficacy Thesaurus, Application Domain, Technology Topic.
© 2024 PatSnap. All rights reserved.Legal|Privacy policy|Modern Slavery Act Transparency Statement|Sitemap