Graphite negative electrode material of low-temperature lithium ion battery and preparation method thereof
A lithium-ion battery, graphite anode technology, applied in battery electrodes, negative electrodes, secondary batteries, etc., can solve problems such as improvement of lithium ion diffusion capacity
- Summary
- Abstract
- Description
- Claims
- Application Information
AI Technical Summary
Problems solved by technology
Method used
Image
Examples
preparation example Construction
[0052] The preparation process of the positive electrode sheet: the positive electrode material LiCoO 2 With PVDF, SP, KS-6 (by mass ratio LiCoO 2 : PVDF: SP: KS-6 = 94.5: 2.5: 2: 1) The dry powder was slowly mixed for 0.5h by a double planetary mixer, and then a certain mass of NMP was added according to the solid-to-liquid ratio of 74%: 26%, and stirred for 6h to make slurry ; The prepared slurry is passed through the coating machine by 20mg cm -2 The mass per unit area is evenly coated on a 16 μm thick aluminum foil, and rolled after drying, where LiCoO 2 The compacted density of the system (mass per unit volume after flat pressing) is 3.9g cm -3 .
[0053] The preparation process of the negative plate: the dry powder of the prepared graphite material and CMC, SBR, SP (composed by mass ratio graphite: CMC: SBR: SP = 92.5: 1.6: 2.4: 3.5) was slowly mixed for 0.5h by a double planetary mixer, Then add a certain quality of deionized water according to the solid-to-liquid rati
Embodiment 1
[0056] Weigh 10g of natural graphite powder and dissolve it in 20mL of deionized water, stir evenly, place it in a ball mill tank, and mill it at a speed of 400r / min for 12h, and use a spray dryer to granulate the ball-milled slurry with an air inlet temperature of 220°C , The air outlet temperature is 120°C; graphite powder is prepared. Graphite powder was mixed with 30 mL of 1 mol / L hydrochloric acid, stirred ultrasonically for 12 h, washed both sides with deionized water, and then dried at 100°C to obtain graphite oxide. Add graphite oxide into 50mL ethanol solution, add nickel acetate intercalation and sodium borohydride reducing agent, ultrasonically disperse for 6 hours, wash with ethanol solution to pH 7, heat-treat the filtered product, and heat it in a tube furnace at 5°C in an argon-hydrogen atmosphere. / min The heating rate is raised to 300°C, and the heat preservation is 6h to obtain the metal nickel intercalated graphite material; the metal nickel intercalated
Embodiment 2
[0058] Weigh 10g of natural graphite powder and dissolve it in 20mL of deionized water, stir evenly, place it in a ball mill tank, and mill it at a speed of 400r / min for 12h, and use a spray dryer to granulate the ball-milled slurry with an air inlet temperature of 220°C , The air outlet temperature is 120°C; graphite powder is prepared. Graphite powder was mixed with 30 mL of 1 mol / L hydrochloric acid, stirred ultrasonically for 12 h, washed both sides with deionized water, and then dried at 100°C to obtain graphite oxide. Add graphite oxide into 50mL ethanol solution, add nickel acetate intercalation and sodium borohydride reducing agent, ultrasonically disperse for 6 hours, wash with ethanol solution to pH 7, heat-treat the filtered product, and heat it in a tube furnace at 5°C in an argon-hydrogen atmosphere. / min The heating rate is raised to 300°C, and the temperature is kept for 6 hours to obtain the metal nickel intercalated graphite material; the metal nickel inter
PUM
Property | Measurement | Unit |
---|---|---|
Thickness | aaaaa | aaaaa |
Particle size | aaaaa | aaaaa |
Granularity | aaaaa | aaaaa |
Abstract
Description
Claims
Application Information
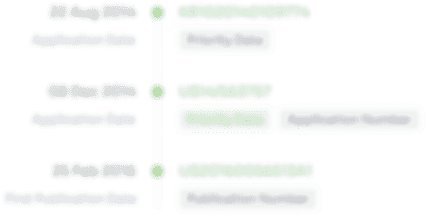
- R&D Engineer
- R&D Manager
- IP Professional
- Industry Leading Data Capabilities
- Powerful AI technology
- Patent DNA Extraction
Browse by: Latest US Patents, China's latest patents, Technical Efficacy Thesaurus, Application Domain, Technology Topic.
© 2024 PatSnap. All rights reserved.Legal|Privacy policy|Modern Slavery Act Transparency Statement|Sitemap