High-toughness co-extrusion barrier film material
A barrier film, high toughness technology, applied in the direction of layered products, synthetic resin layered products, chemical instruments and methods, etc., can solve the problems of low strength, low barrier performance, and high breakage rate, so as to improve the barrier performance, increase mechanical stability, and save social resources
- Summary
- Abstract
- Description
- Claims
- Application Information
AI Technical Summary
Problems solved by technology
Method used
Examples
Example Embodiment
[0009] Example 1
[0010] A high-toughness co-extruded barrier film material. The film has a layered structure. The layers are 21% polyethylene PE layer, 15% metallocene polyethylene layer, 5% TiC adhesive layer, 18% ethylene -Vinyl alcohol copolymer EVOH barrier layer, 5% TiC adhesive layer, 15% metallocene polyethylene layer and 21% polyethylene PE layer. Each layer of the film is formed by a co-extrusion process.
Example Embodiment
[0011] Example 2
[0012] A high-toughness co-extrusion barrier film material, the film is a layered structure, each layer is 15% polyethylene PE layer, 10% metallocene polyethylene layer, 5% TiC adhesive layer, 5% ethylene -Vinyl alcohol copolymer EVOH barrier layer, 5% TiC adhesive layer, 10% metallocene polyethylene layer and 15% polyethylene PE layer. Each layer of the film is formed by a co-extrusion process.
Example Embodiment
[0013] Example 3
[0014] A high-toughness co-extrusion barrier film material. The film has a layered structure. The layers are 60% polyethylene PE layer, 50% metallocene polyethylene layer, 5% TiC adhesive layer, and 25% ethylene. -Vinyl alcohol copolymer EVOH barrier layer, 5% TiC adhesive layer, 50% metallocene polyethylene layer and 60% polyethylene PE layer. Each layer of the film is formed by a co-extrusion process.
PUM
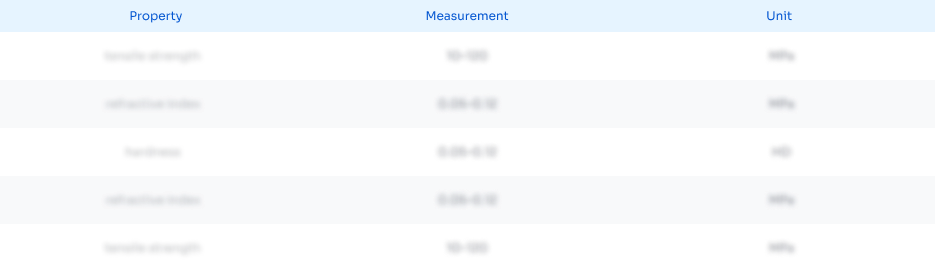
Abstract
Description
Claims
Application Information
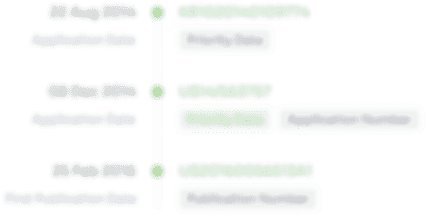
- R&D Engineer
- R&D Manager
- IP Professional
- Industry Leading Data Capabilities
- Powerful AI technology
- Patent DNA Extraction
Browse by: Latest US Patents, China's latest patents, Technical Efficacy Thesaurus, Application Domain, Technology Topic.
© 2024 PatSnap. All rights reserved.Legal|Privacy policy|Modern Slavery Act Transparency Statement|Sitemap