Antistatic shielding aluminum-plastic composite packaging material
An aluminum-plastic composite and packaging material technology, applied in the field of packaging materials, can solve the problems of aluminum foil damage, no antistatic shielding, poor folding resistance, impact resistance and puncture resistance of aluminum foil, and achieve the effect of improving the ability
- Summary
- Abstract
- Description
- Claims
- Application Information
AI Technical Summary
Benefits of technology
Problems solved by technology
Method used
Examples
Embodiment 1
[0014] An antistatic shielding aluminum-plastic composite packaging material, an outer protective layer, an outer adhesive layer, an antistatic coating, an aluminum foil layer, an outer adhesive layer A, a nylon film, and an outer adhesive layer are sequentially arranged from the outside to the inside Layer B and heat-sealing layer; the antistatic coating includes the following components by weight: 42 parts of synthetic acrylic resin, 50 parts of epoxy resin, 20 parts of diatomaceous earth, 20 parts of graphite with a purity of more than 99%, dispersant 0.5 parts, 2 parts of defoamer, 3 parts of thickener; The outer protective layer comprises the following components by weight: 40 parts of ethoxylated trimethylolpropane triacrylate, 25 parts of polyamide wax, di-n-hexylamine 16 parts, 75 parts of thermoplastic polyurethane elastomer, 2 parts of benzimidazole, 6 parts of lubricant, 35 parts of random copolymerized polypropylene, 1 part of epoxy cottonseed oil, 12 parts of sulfoeth
Embodiment 2
[0016] An antistatic shielding aluminum-plastic composite packaging material, an outer protective layer, an outer adhesive layer, an antistatic coating, an aluminum foil layer, an outer adhesive layer A, a nylon film, and an outer adhesive layer are sequentially arranged from the outside to the inside Layer B and the heat-sealing layer; the antistatic coating includes the following components by weight: 55 parts of synthetic acrylic resin, 60 parts of epoxy resin, 35 parts of diatomaceous earth, 28 parts of graphite with a purity of more than 99%, dispersant 1.3 parts, 4 parts of defoaming agent, 5 parts of thickening agent; Described outer protective layer comprises the component of following parts by weight: ethoxylated trimethylolpropane triacrylate 60 parts, polyamide wax 35 parts, di-n-hexylamine 28 parts, 88 parts of thermoplastic polyurethane elastomer, 5 parts of benzimidazole, 11 parts of lubricant, 47 parts of random copolymer polypropylene, 19 parts of epoxy cottonseed
Embodiment 3
[0018] An antistatic shielding aluminum-plastic composite packaging material, an outer protective layer, an outer adhesive layer, an antistatic coating, an aluminum foil layer, an outer adhesive layer A, a nylon film, and an outer adhesive layer are sequentially arranged from the outside to the inside Layer B and the heat-sealing layer; the antistatic coating includes the following components by weight: 54 parts of synthetic acrylic resin, 59 parts of epoxy resin, 34 parts of diatomaceous earth, 27 parts of graphite with a purity of more than 99%, dispersant 1.2 parts, 3.9 parts of defoaming agent, 4.9 parts of thickening agent; Described outer protection layer comprises the component of following parts by weight: ethoxylated trimethylolpropane triacrylate 59 parts, polyamide wax 34 parts, di-n-hexylamine 27 parts, 87 parts of thermoplastic polyurethane elastomer, 4.9 parts of benzimidazole, 10 parts of lubricant, 46 parts of random copolymerized polypropylene, 8 parts of epoxy co
PUM
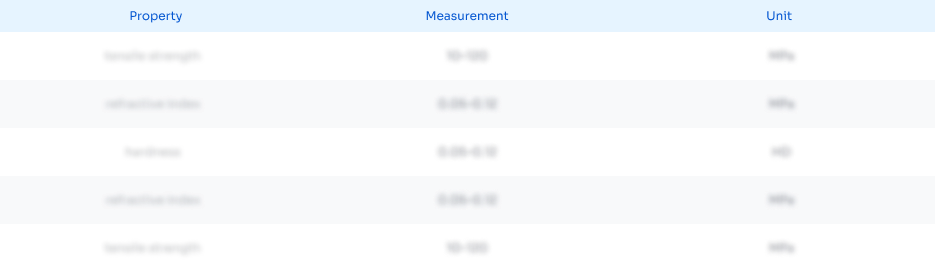
Abstract
Description
Claims
Application Information
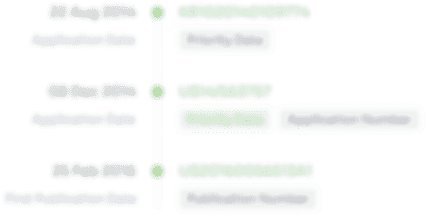
- R&D Engineer
- R&D Manager
- IP Professional
- Industry Leading Data Capabilities
- Powerful AI technology
- Patent DNA Extraction
Browse by: Latest US Patents, China's latest patents, Technical Efficacy Thesaurus, Application Domain, Technology Topic.
© 2024 PatSnap. All rights reserved.Legal|Privacy policy|Modern Slavery Act Transparency Statement|Sitemap