Preparation method of porous pollucite profile
A cesium zeolite and profile technology, which is applied in the field of preparation of functional material profiles, can solve the problems of product structure and performance changes, difficulty, complex preparation process, etc., and achieve the effect of good performance, simple equipment and process, and mild preparation conditions
- Summary
- Abstract
- Description
- Claims
- Application Information
AI Technical Summary
Problems solved by technology
Method used
Image
Examples
Embodiment 1
[0027] A preparation method of a porous cesium zeolite profile, the steps are: according to the weight ratio of 100 parts by weight of metakaolin, 75 parts by weight of amorphous spherical silica ultrafine powder, and 145 parts by weight of cesium hydroxide monohydrate Kaolin, amorphous spherical silicon dioxide superfine powder and cesium hydroxide monohydrate, mixed uniformly; water is taken according to 20% of the total weight of solid raw material metakaolin, amorphous spherical silicon dioxide superfine powder and cesium hydroxide monohydrate , added to the solid raw material, stirred evenly to obtain a slurry; inject the slurry into a steel mold, seal it at room temperature, place it in a blast drying oven at 50-100°C for 24 hours, and then demould to obtain a solid profile; Put it in an autoclaved reaction kettle, and after hydrothermal reaction in a water vapor environment at a temperature of 180°C for 20 hours, take it out and dry it in a blast drying oven at 105°C for 24
Embodiment 2
[0029] A preparation method of a porous cesium zeolite profile, the steps are: according to the weight ratio of 100 parts by weight of metakaolin, 110 parts by weight of amorphous spherical silica ultrafine powder, and 145 parts by weight of cesium hydroxide monohydrate Kaolin, amorphous spherical silicon dioxide superfine powder and cesium hydroxide monohydrate, mixed uniformly; water is taken according to 20% of the total weight of solid raw material metakaolin, amorphous spherical silicon dioxide superfine powder and cesium hydroxide monohydrate , added to the solid raw material, stirred evenly to obtain a slurry; inject the slurry into a steel mold, seal it at room temperature, place it in a blast drying oven at 50-100°C for 24 hours, and then demould to obtain a solid profile; Put it in an autoclaved reaction kettle, and after hydrothermal reaction in a water vapor environment at a temperature of 180°C for 20 hours, take it out and dry it in a blast drying oven at 105°C for 2
Embodiment 3
[0031]A preparation method of a porous cesium zeolite profile, the steps are: according to the weight ratio of 100 parts by weight of metakaolin, 155 parts by weight of amorphous spherical silica ultrafine powder, and 145 parts by weight of cesium hydroxide monohydrate Kaolin, amorphous spherical silicon dioxide superfine powder and cesium hydroxide monohydrate, mixed uniformly; water is taken according to 20% of the total weight of solid raw material metakaolin, amorphous spherical silicon dioxide superfine powder and cesium hydroxide monohydrate , added to the solid raw material, stirred evenly to obtain a slurry; inject the slurry into a steel mold, seal it at room temperature, place it in a blast drying oven at 50-100°C for 24 hours, and then demould to obtain a solid profile; Put it in an autoclaved reaction kettle, and after hydrothermal reaction in a water vapor environment at a temperature of 180°C for 20 hours, take it out and dry it in a blast drying oven at 105°C for 24
PUM
Property | Measurement | Unit |
---|---|---|
Diameter | aaaaa | aaaaa |
Compressive strength | aaaaa | aaaaa |
Apparent density | aaaaa | aaaaa |
Abstract
Description
Claims
Application Information
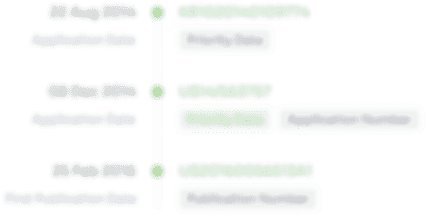
- R&D Engineer
- R&D Manager
- IP Professional
- Industry Leading Data Capabilities
- Powerful AI technology
- Patent DNA Extraction
Browse by: Latest US Patents, China's latest patents, Technical Efficacy Thesaurus, Application Domain, Technology Topic.
© 2024 PatSnap. All rights reserved.Legal|Privacy policy|Modern Slavery Act Transparency Statement|Sitemap