Method for recovering alkali, selenium and arsenic in arsenic-alkali residue from antimony smelting
A technology of arsenic-alkali slag and arsenic-alkali slag, which is applied in the field of antimony smelting arsenic-alkali slag disposal, selenium and arsenic, and recovery of alkali from arsenic-alkali slag, which can solve the problem of unrealized component recovery, unstable product components, and affecting glass quality and other issues, to achieve good economic and environmental benefits, high utilization, and reduce production costs
- Summary
- Abstract
- Description
- Claims
- Application Information
AI Technical Summary
Problems solved by technology
Method used
Examples
Example Embodiment
[0034] Example 1
[0035] The method is used to treat secondary arsenic-alkali slag from an antimony smelter in Hunan, and the water content of the arsenic-alkali slag is 31.2%. Crush the arsenic slag to less than 5mm, then take 1.2 kg of arsenic slag and leaching with water at a liquid-to-solid ratio of 3mL / g, stirring speed 100r / min and leaching temperature of 95℃ for 1h, filter and wash to obtain antimony slag and arsenic alkali Solution. The alkali leaching rate of the arsenic-alkali residue leaching and washing process was 100%, and the leaching rates of As, Sb and Se were 98.4%, 1.8% and 97.9%, respectively. Table 1 shows the content of related components in arsenic-base slag and antimony slag (dry basis), and Table 2 shows the content of related components in arsenic-base solution.
[0036] Table 1 Contents of related components of arsenic-alkali slag and antimony slag (%)
[0037]
[0038] Table 2 Contents of relevant components in arsenic alkali solution (g / L)
[0039]
Example Embodiment
[0049] Example 2
[0050] The experimental conditions of the arsenic slag, arsenic slag leaching and washing, and the twice recovery of alkali with carbon dioxide used in this example are the same as in Example 1. Adjust the pH of the secondary crystallization mother liquor to 2.9 with sulfuric acid, heat it to 100°C for 20 minutes, and filter while it is hot to obtain black selenium and de-selenium liquid. The direct yield of selenium is 81.3%. The content of related components in black selenium is shown in Table 4. Show. CO produced during pH adjustment by sulfuric acid 2 Return to the alkali recovery process for recycling.
[0051] After removing selenium, the solution is fed with SO at 25℃ and stirring speed 200r / min 2 Reducing As(V) to As(III), then concentrating the reduced liquid by 3.8 times, then cooling and crystallizing at 25℃, and filtering to obtain crude arsenic trioxide and the liquid after arsenic removal. The direct arsenic yield is 80.7%. After arsenic removal Th
Example Embodiment
[0054] Example 3
[0055] The method is used to treat the secondary arsenic-alkali slag from an antimony smelter in Hunan, and the water content of the arsenic-alkali slag is 29.1%. The arsenic slag is crushed to below 5mm, and then 1.2kg of arsenic slag is leached with water at a liquid-solid ratio of 3.5mL / g, stirring speed 100r / min and leaching temperature 105℃ for 1h, filtered and washed to obtain antimony slag and arsenic alkali Solution. The leaching rate of arsenic-alkali residue in the leaching and washing process was 100%, and the leaching rates of As, Sb and Se were 99.4%, 2.1% and 98.9%, respectively. Table 5 shows the content of related components in arsenic-base slag and antimony slag (dry basis), and Table 6 shows the content of related components in arsenic-base solution.
[0056] Table 5 Contents of related components of arsenic-alkali slag and antimony slag (%)
[0057]
[0058] Table 6 Contents of relevant components in arsenic-alkali mixture (g / L)
[0059]
[
PUM
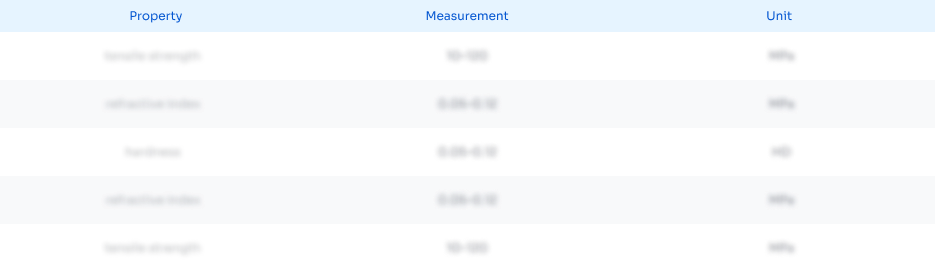
Abstract
Description
Claims
Application Information
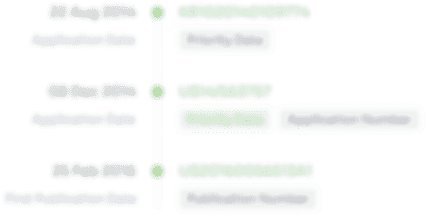
- R&D Engineer
- R&D Manager
- IP Professional
- Industry Leading Data Capabilities
- Powerful AI technology
- Patent DNA Extraction
Browse by: Latest US Patents, China's latest patents, Technical Efficacy Thesaurus, Application Domain, Technology Topic.
© 2024 PatSnap. All rights reserved.Legal|Privacy policy|Modern Slavery Act Transparency Statement|Sitemap