Fireproof wear-resistant fabric
A wear-resistant fabric and modification technology, which is applied in the field of textile fabrics, can solve the problems of affecting performance, forming molten droplets, and restricting the application of polyester products, etc., and achieves the effect of excellent mechanical stretching
- Summary
- Abstract
- Description
- Claims
- Application Information
AI Technical Summary
Benefits of technology
Problems solved by technology
Method used
Image
Examples
preparation example Construction
[0076] The preparation method of described polyditrimethylolpropanethiophosphorylurea (PDTPT), comprises the following steps:
[0077] (1) Synthesis of intermediate ditrimethylolpropane diphosphoryl chloride (DTDC)
[0078] Add a certain proportion of ditrimethylolpropane (DTMP) and solvent dichloroethane into the four-neck flask, slowly raise the temperature to 40°C under electric stirring, and add POCl after DTMP is completely dissolved 3 , and use lye to absorb the HCl gas produced by the reaction, keep it warm for 6 hours, cool to room temperature after the reaction, and distill off the solvent dichloroethane and unreacted POCl under reduced pressure 3 , to obtain a white solid crude product, after adding a certain amount of absolute ethanol, put it in a freezer (-20°C) for 2 hours, filter and vacuum dry the obtained white solid at 70°C to constant weight, and then obtain a white powdery solid DTDC .
[0079] (2) Synthesis of polyditrimethylolpropanethiophosphorylurea (PDTP
Embodiment 1
[0129] Embodiment 1 provides a fire-resistant and wear-resistant fabric, which is made of polyethylene terephthalate and modified graphene blended yarn woven into a base fabric, which is prepared after being treated with a finishing solution.
[0130] The modifying agent is N-[3-[three(2-methoxyethoxy)silyl]propyl]ethane-1,2-diamine; the graphene oxide and N-[3- The mass ratio of [tris(2-methoxyethoxy)silyl]propyl]ethane-1,2-diamine is 1:1.
[0131] In the preparation method of described modified graphene oxide, the quality of modifying agent is 5g.
[0132] The mass ratio of described polyethylene terephthalate and modified graphene oxide is 100:0.1; In described polyethylene terephthalate and modified graphene oxide blend spinning process, by mass Parts, 100 parts of polyethylene terephthalate, 0.1 part of modified graphene oxide.
[0133] The finishing liquid comprises polyditrimethylolpropane thiophosphoryl urea and trimethylsilicate cage thioPEPA ester; The mass ratio of
Embodiment 2
[0137] Embodiment 2 provides a fire-resistant and wear-resistant fabric, which is made of polyethylene terephthalate and modified graphene blended yarn woven into a base fabric, which is prepared after being treated with a finishing solution.
[0138] The modifying agent is N-[3-[three(2-methoxyethoxy)silyl]propyl]ethane-1,2-diamine; the graphene oxide and N-[3- The mass ratio of [tris(2-methoxyethoxy)silyl]propyl]ethane-1,2-diamine is 1:3.
[0139] In the preparation method of described modified graphene oxide, the quality of modifying agent is 15g.
[0140] The mass ratio of described polyethylene terephthalate and modified graphene oxide is 100:1.5; In described polyethylene terephthalate and modified graphene oxide blend spinning process, by mass Parts, 100 parts of polyethylene terephthalate, 1.5 parts of modified graphene oxide.
[0141] The finishing liquid comprises polyditrimethylolpropane thiophosphoryl urea and trimethylsilicate cage thioPEPA ester; The mass ratio o
PUM
Property | Measurement | Unit |
---|---|---|
Concentration | aaaaa | aaaaa |
Abstract
Description
Claims
Application Information
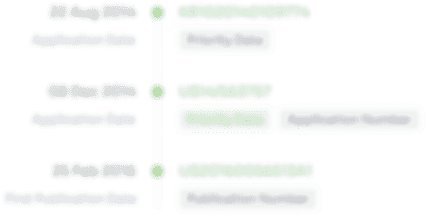
- R&D Engineer
- R&D Manager
- IP Professional
- Industry Leading Data Capabilities
- Powerful AI technology
- Patent DNA Extraction
Browse by: Latest US Patents, China's latest patents, Technical Efficacy Thesaurus, Application Domain, Technology Topic.
© 2024 PatSnap. All rights reserved.Legal|Privacy policy|Modern Slavery Act Transparency Statement|Sitemap