Coiled tubing pipe-to-pipe butt joint process and raw material thickening equipment thereof
A technology for oil pipe joints and oil pipes, which is applied in the direction of metal processing equipment, etc., can solve problems such as oxidation burning, welding collapse, and affecting the performance of pipe butt joints, etc., to achieve improved hammering strength, uniform deformation, and uniform hammering force Effect
- Summary
- Abstract
- Description
- Claims
- Application Information
AI Technical Summary
Benefits of technology
Problems solved by technology
Method used
Image
Examples
Embodiment Construction
[0030] The core of the present invention is to provide a coiled tubing butt jointing process and its raw material thickening equipment, which can effectively reduce edge burning and collapse during the welding process, and improve the welding quality of the pipe butt joint.
[0031] The technical solutions in the embodiments of the present invention will be clearly and completely described below in conjunction with the accompanying drawings in the embodiments of the present invention. Obviously, the described embodiments are only some of the embodiments of the present invention, not all of them. Based on the embodiments of the present invention, all other embodiments obtained by persons of ordinary skill in the art without making creative efforts belong to the protection scope of the present invention.
[0032] With reference to the accompanying drawings, figure 1 It is a schematic diagram of the pipe butt joint process flow of the present invention; figure 2 It is a schematic
PUM
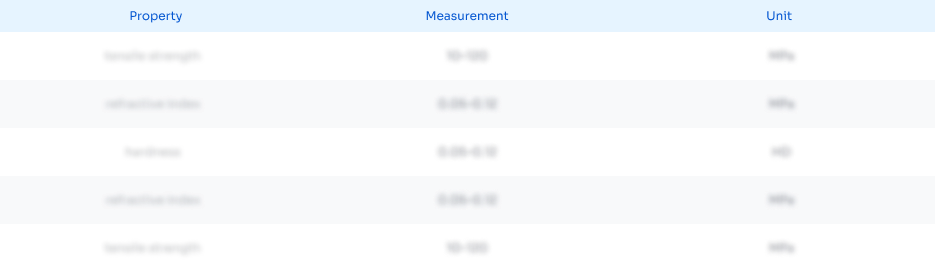
Abstract
Description
Claims
Application Information
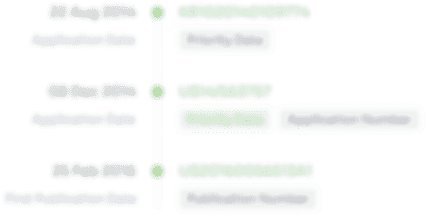
- R&D Engineer
- R&D Manager
- IP Professional
- Industry Leading Data Capabilities
- Powerful AI technology
- Patent DNA Extraction
Browse by: Latest US Patents, China's latest patents, Technical Efficacy Thesaurus, Application Domain, Technology Topic.
© 2024 PatSnap. All rights reserved.Legal|Privacy policy|Modern Slavery Act Transparency Statement|Sitemap