PMMA-aluminum hydroxide-organophosphorus acrylic composite base material and preparation method thereof
A technology of aluminum hydroxide and composite substrate, applied in the field of artificial stone, can solve the problems of large oil absorption, increased cost, low flame retardant efficiency and other problems, and achieve the effect of excellent flame retardancy and low cost
- Summary
- Abstract
- Description
- Claims
- Application Information
AI Technical Summary
Benefits of technology
Problems solved by technology
Method used
Examples
Embodiment 1
[0022] S1. Add 80 kg of 20-micron aluminum hydroxide powder into the mixing mixer. When the temperature of the aluminum hydroxide powder reaches 90-120°C, directly add the methacryloyl silane coupling agent in 0.4 kg of silane coupling agent: 3 -(Methacryloyloxy)propyltrimethoxysilane KH570 (Guangzhou Zhongjie Chemical Technology Co., Ltd.), 0.4 kg isopropyl tris(dioctylpyrophosphate acyloxy) titanate coupling agent PN- 41B (Nanjing Pinning Coupling Agent Co., Ltd.) was added and mixed continuously for 20 minutes to prepare superfine aluminum hydroxide microspheres with surface hydrophobic modification;
[0023] S2. Add 95 kilograms of methyl methacrylate, 1 kilogram of methacrylic acid as a comonomer, 1.5 kilograms of ethylene glycol dimethacrylate and 2.5 kilograms of phosphorus-containing methacrylate into the polymerization reactor. At 65-75°C, start to add 20 grams of azobisisobutyronitrile initiator for polymerization reaction, and keep the temperature in the kettle at 80-9
Embodiment 2
[0026] S1. Add 90 kg of 30-micron aluminum hydroxide powder into the mixing mixer. When the temperature of the aluminum hydroxide powder reaches 90-120°C, directly add 0.5 kg of vinyltrimethoxyethoxysilane A172 (Guangzhou Zhongjie Chemical Co., Ltd. Technology Co., Ltd.), 0.5 kg of isopropyl tris (dioctyl pyrophosphate acyloxy) titanate coupling agent PN-41B (Nanjing Pinning Coupling Agent Co., Ltd.) was added and continuously mixed for 30 minutes to obtain Surface hydrophobic modified aluminum hydroxide ultrafine microspheres;
[0027] S2. Add 90 kilograms of methyl methacrylate, 4 kilograms of methacrylic acid as comonomers, 2 kilograms of trimethylolpropane trimethacrylate and 3 kilograms of phosphorus-containing methacrylate into the polymerization reactor, and when the reactor When internally heated to 65-75°C, start to add 15 grams of azobisisobutyronitrile initiator for polymerization reaction, and keep the temperature in the kettle at 80-90°C for about 2 hours to obtain 1
Embodiment 3
[0030] S1. Add 100 parts of 20-micron aluminum hydroxide powder into the mixing mixer. When the temperature of the aluminum hydroxide powder reaches 90-120°C, add 2 parts of vinyltrimethoxyethoxysilane coupling agent A172 (Guangzhou City Center Jie Chemical Technology Co., Ltd.), 2 parts of isopropyl tris (dioctyl pyrophosphate acyloxy) titanate coupling agent PN-41B (Nanjing Pinning Coupling Agent Co., Ltd.) were added to the aluminum hydroxide powder and continuously Mix and stir for 10-30 minutes to prepare surface hydrophobic modified aluminum hydroxide ultrafine microspheres;
[0031] S2. Add 75 parts of methyl methacrylate, 10 parts of methacrylic acid, 5 parts of ethylene glycol dimethacrylate and 10 parts of phosphorus-containing methacrylate into the polymerization reaction kettle. When the kettle is heated to 65-75 At ℃, start to add 200g of azobisisobutyronitrile initiator for polymerization reaction, and keep the temperature in the kettle at 80-95℃ for about 2.5 hours
PUM
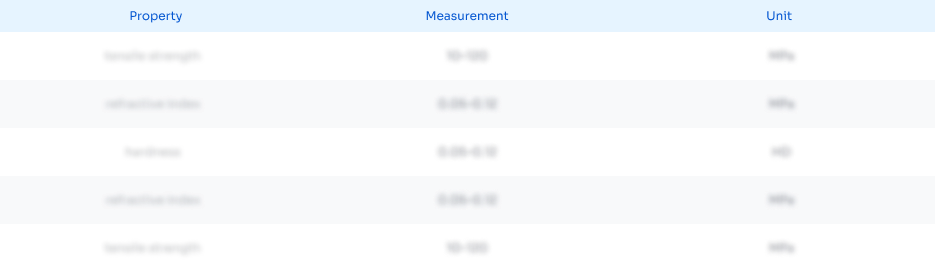
Abstract
Description
Claims
Application Information
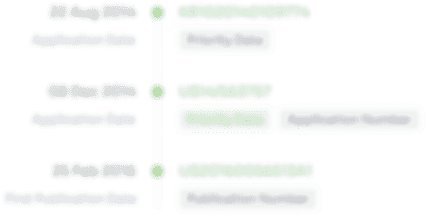
- R&D Engineer
- R&D Manager
- IP Professional
- Industry Leading Data Capabilities
- Powerful AI technology
- Patent DNA Extraction
Browse by: Latest US Patents, China's latest patents, Technical Efficacy Thesaurus, Application Domain, Technology Topic.
© 2024 PatSnap. All rights reserved.Legal|Privacy policy|Modern Slavery Act Transparency Statement|Sitemap