Hot-dip galvanized plate suitable for low-temperature environment for gas meter shell and production method thereof
A technology for instrument shells and production methods, applied in hot-dip plating process, manufacturing converters, coatings, etc., which can solve the problems of poor formability, high cost, and high product strength
- Summary
- Abstract
- Description
- Claims
- Application Information
AI Technical Summary
Problems solved by technology
Method used
Image
Examples
Embodiment 1
[0079] The metallographic structure of embodiment 1 is as figure 1 As shown, the inclusion ratings of the examples and comparative examples are shown in Table 4. It can be seen that the metallographic structure of the example is ferrite, the grain size is 8.0, and there are few inclusions in the substrate of the example, as shown in Table 4.
[0080] Table 4 Inclusion Ratings of Examples 1-4 and Comparative Examples 1-3
[0081] category A thin A rough B thin B thick C thin C thick D thin D thick DS Example 1 0 0 0 0 0 0 0.5 0 0 Example 2 0 0 0.5 0 0 0 0 0 0 Example 3 0 0 0 0 0 0 0.5 0 0 Example 4 0 0 0.5 0 0 0 0 0 0 Comparative example 1 0 0.5 0 1.0 0 0 0 1.0 0.5 Comparative example 2 1.5 0 1.0 0 0 0 1.0 0 0.5 Comparative example 3 0.5 0 1.0 0 0 0 0.5 0 0.5
[0082] After the formed part was placed at low temperature for 5 hours, a 6kg lead ball was
PUM
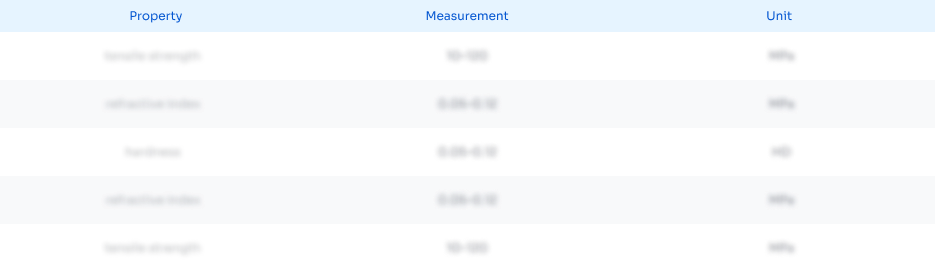
Abstract
Description
Claims
Application Information
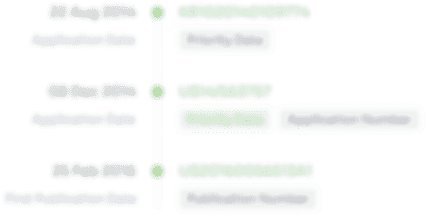
- R&D Engineer
- R&D Manager
- IP Professional
- Industry Leading Data Capabilities
- Powerful AI technology
- Patent DNA Extraction
Browse by: Latest US Patents, China's latest patents, Technical Efficacy Thesaurus, Application Domain, Technology Topic.
© 2024 PatSnap. All rights reserved.Legal|Privacy policy|Modern Slavery Act Transparency Statement|Sitemap