Electric heating glass of novel structure and manufacturing method
A technology for electrically heating glass and a new structure, applied in the direction of heating element materials, etc., can solve the problems of glass breakage, wire falling off, glass cannot withstand high temperature, etc., and achieve the effect of improving the yield and increasing the firmness.
- Summary
- Abstract
- Description
- Claims
- Application Information
AI Technical Summary
Problems solved by technology
Method used
Examples
Example Embodiment
[0025] The present invention will be described in detail below in conjunction with the drawings and specific implementations:
[0026] Such as figure 1 As shown, figure 1 It is a schematic diagram of the structure of traditional electrically heated glass. The traditional electrically heated glass includes a glass body 1. A copper foil is pasted on the glass body 1, and then the wire is welded to the copper foil. This will increase the resistance between the two poles, resulting in The heating power is insufficient to achieve the required temperature rise within the specified time; and because the glass body 1 cannot withstand high temperatures, during welding, the welding temperature is as high as 400 ℃, which may easily cause the glass to break; also because there is only one solder joint , During the assembly process, it is easy to cause the wire to fall off.
[0027] figure 2 with image 3 It is a schematic diagram of the structure of the present invention, including a glass plat
PUM
Property | Measurement | Unit |
---|---|---|
Width | aaaaa | aaaaa |
Abstract
Description
Claims
Application Information
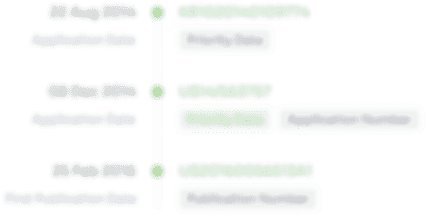
- R&D Engineer
- R&D Manager
- IP Professional
- Industry Leading Data Capabilities
- Powerful AI technology
- Patent DNA Extraction
Browse by: Latest US Patents, China's latest patents, Technical Efficacy Thesaurus, Application Domain, Technology Topic.
© 2024 PatSnap. All rights reserved.Legal|Privacy policy|Modern Slavery Act Transparency Statement|Sitemap