Ammoxidation catalyst and preparation method and application thereof
A technology of ammoxidation reaction and catalyst, applied in the direction of preparation of hydrocarbon ammoxidation, physical/chemical process catalyst, metal/metal oxide/metal hydroxide catalyst, etc. Reducing the yield, increasing the cost of three wastes treatment and environmental protection, and increasing the cost of raw materials, etc., to achieve the effect of improving the reaction activity, reducing the activation energy of the reaction, and reducing the amount of use
- Summary
- Abstract
- Description
- Claims
- Application Information
AI Technical Summary
Benefits of technology
Problems solved by technology
Method used
Examples
Embodiment 1
[0051] 1) Heat 2500g of water to 85°C, and stir 1950g of oxalic acid (H 2 C 2 o 4 ) was added into water to form an aqueous oxalic acid solution; 455g vanadium pentoxide, 680g silver nitrate and 1360g arsenic trichloride were added to 680g water to form a reaction solution one;
[0052] Under stirring, the above-mentioned reaction solution 1 was added to the oxalic acid aqueous solution to form a mixed solution 1;
[0053] 2) 1074g manganese nitrate, 1073g zirconium nitrate pentahydrate and 8.7g rhodium nitrate were dissolved in 3918.3g water to form reaction solution two;
[0054] Add 2750 g of silica sol with a mass percentage of 40% and the above-mentioned reaction solution 2 to the mixed solution 1 to obtain the mixed solution 2;
[0055] 3) Stir the above mixed solution 2 at 90°C at a speed of 350rpm for 200min, then raise the temperature to 105°C and let stand for 60min for aging treatment, and evaporate the solution after aging treatment to a slurry with a solid content
Embodiment 2
[0062] 1) Heat 2550g of water to 75°C, and stir 2000g of oxalic acid (H 2 C 2 o 4 ) was added into water to form an aqueous oxalic acid solution; 455g of vanadium pentoxide, 765g of silver nitrate and 1269g of arsenic trichloride were added to 780g of water to form a reaction solution 1;
[0063] Under stirring, the above-mentioned reaction solution 1 was added to the oxalic acid aqueous solution to form a mixed solution 1;
[0064] 2) 1988g of lead nitrate, 293g of cesium nitrate and 12.4g of iridium trichloride hydrate were dissolved in 4594.6g of water to form reaction solution 2;
[0065] Add 2800 g of silica sol with a mass percentage of 40% and the above-mentioned reaction solution 2 to the mixed solution 1 to obtain the mixed solution 2;
[0066] 3) Stir the above mixed solution 2 at 85°C at a speed of 300rpm for 180min, then raise the temperature to 108°C and let stand for 75min for aging treatment, and evaporate the solution after aging treatment to a slurry with a so
Embodiment 3
[0073] 1) Heat 2600g of water to 80°C, and stir 2100g of oxalic acid (H 2 C 2 o 4 ) was added into water to form an aqueous oxalic acid solution; 455g of vanadium pentoxide, 510g of silver nitrate and 998g of arsenic trichloride were added to 800g of water to form a reaction solution 1;
[0074] Under stirring, the above-mentioned reaction solution 1 was added to the oxalic acid aqueous solution to form a mixed solution 1;
[0075] 2) 1190g zinc nitrate hexahydrate, 1519g cerium nitrate hexahydrate and 16.85g platinum chloride were dissolved in 3513.15g water to form reaction solution 2;
[0076] Add 3000 g of silica sol with a mass percentage of 40% and the above-mentioned reaction solution 2 to the mixed solution 1 to obtain the mixed solution 2;
[0077] 3) Stir the above mixed solution 2 at 90°C at a speed of 310rpm for 150min, then raise the temperature to 110°C and let stand for 180min for aging treatment, and evaporate the solution after aging treatment to a slurry with
PUM
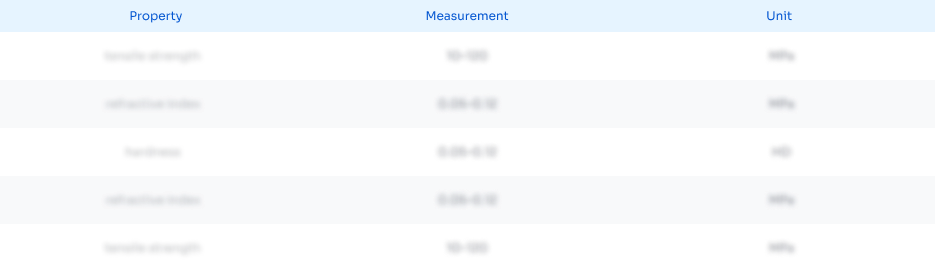
Abstract
Description
Claims
Application Information
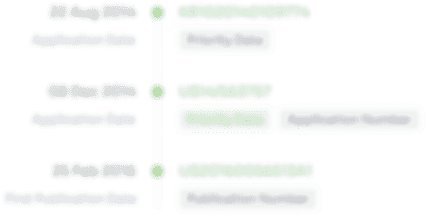
- R&D Engineer
- R&D Manager
- IP Professional
- Industry Leading Data Capabilities
- Powerful AI technology
- Patent DNA Extraction
Browse by: Latest US Patents, China's latest patents, Technical Efficacy Thesaurus, Application Domain, Technology Topic.
© 2024 PatSnap. All rights reserved.Legal|Privacy policy|Modern Slavery Act Transparency Statement|Sitemap