Manufacturing process of boiler dust collection device
The invention relates to a technology of a vacuum cleaner and a manufacturing process, which is applied to the manufacturing process of a boiler dust collector, and can solve the problems of unstable device, easily damaged cloth bags, low work efficiency, etc., so as to improve the efficiency, reduce the difficulty of production, and prolong the use of the dust collector. effect of life
- Summary
- Abstract
- Description
- Claims
- Application Information
AI Technical Summary
Problems solved by technology
Method used
Examples
Example Embodiment
[0031] The first embodiment is basically as attached figure 1 , figure 2 Shown:
[0032] A manufacturing process of a boiler dust collection device. The process steps for manufacturing a boiler dust collection device are:
[0033] The boiler dust collection device includes a frame 1. The frame 1 is fixedly connected with a box body 2 through bolts, the box body 2 is provided with an exhaust port 3, the box body 2 is fixedly connected with a cloth bag 4, and the bottom of the box body 2 is connected There is an ash hopper 5, the bottom of the ash hopper 5 is provided with a dust discharge port 6, and a valve 7 is installed on the dust discharge port 6. The side wall of the ash hopper 5 is provided with an air inlet 8 that slopes downward along the inner wall of the ash hopper 5. The number of ports 8 is an odd number greater than one, and the air intake ports 8 are distributed in a circular array on the inner wall of the ash hopper 5.
[0034] The frame 1 is provided with a cooling mec
Example Embodiment
[0040] The second embodiment is basically as attached image 3 Shown:
[0041] The difference between this embodiment and the first embodiment is that the cooling mechanism further includes a plurality of spray heads 17 arranged in the box body 2. The spray heads 17 are located under the cloth bag 4 and are distributed in a circular array on the side wall of the box body 2. 2 is fixedly connected to a water tank 18, and a conduit is connected between the water tank 18 and the nozzle 17, and a one-way valve that is one-way to the tank 2 is installed on the conduit. A water pump is installed in the water tank 18 to pump the water in the water tank 18 Into the pipe, the water is sprayed from the nozzle 17. A water pipe 19 is connected between the water tank 18 and the water outlet 14, and a three-way valve 20 is installed on the water pipe 19. A first filter mesh 21 and a second filter mesh 22 are fixed in the box body 2 by bolts. The cloth bag 4 is located between the first filter m
PUM
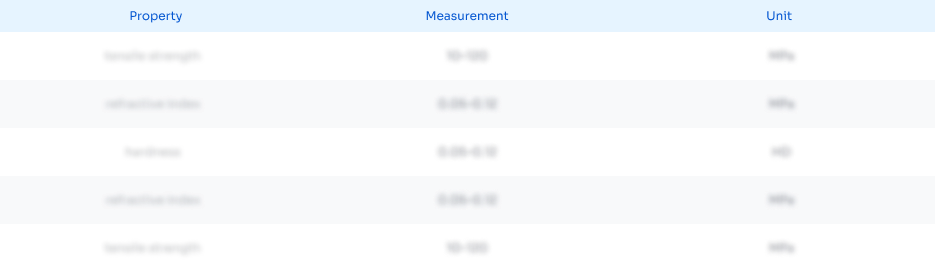
Abstract
Description
Claims
Application Information
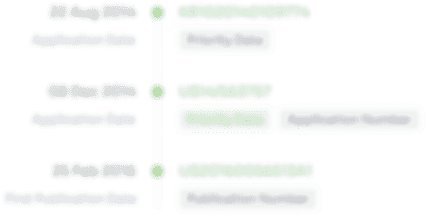
- R&D Engineer
- R&D Manager
- IP Professional
- Industry Leading Data Capabilities
- Powerful AI technology
- Patent DNA Extraction
Browse by: Latest US Patents, China's latest patents, Technical Efficacy Thesaurus, Application Domain, Technology Topic.
© 2024 PatSnap. All rights reserved.Legal|Privacy policy|Modern Slavery Act Transparency Statement|Sitemap