Appearance self-adaptive flexible transfer robot and material management application system
A handling robot and self-adaptive technology, which is applied in data processing applications, transport objects, signal transmission systems, etc., can solve the problems of safety hazards, heavy labor, and low work efficiency for handling personnel, and achieve the realization of material handling and automation. High, overcoming the effect of a large amount of labor
- Summary
- Abstract
- Description
- Claims
- Application Information
AI Technical Summary
Benefits of technology
Problems solved by technology
Method used
Image
Examples
Embodiment 1
[0041] Such as figure 1 , figure 2 As shown, a shape-adaptive and flexible handling robot includes a plurality of frames 1, a telescopic support beam 2 that is connected to the frames 1 in turn to form a rectangular structure, a walking mechanism 3 that drives the frames 1 to move synchronously, and is installed on On the vehicle frame 1 and can realize the carrying mechanism 4 of lifting.
[0042] In the present embodiment, vehicle frame 1 selects four altogether, and is arranged at the four apex places that can enclose rectangular structure, and this vehicle frame 1 comprises the first lower frame body 11 and the first upper frame body 12; The mecanum wheel 31 is installed on the side of the first lower frame body 11 and is driven by a servo motor 301 .
[0043] combine figure 2 , image 3 As shown, the telescopic support beam 2 includes a first connecting beam 21 and an electric cylinder 22 that drives the first connecting beam 21 to expand and contract; It is driven to
Embodiment 2
[0049] The difference between this embodiment and Embodiment 1 lies in: combining Figure 6 , Figure 7 As shown, the running gear 3 selects the steering wheel, and now the telescopic support beam 2 adopts the second connecting beam 23 and the optical axis 24 coaxially arranged, and the optical axis 24 and the second connecting beam 23 are plugged and movably connected.
[0050] More specifically, the vehicle frame 1 includes a second lower frame body 13 and a second upper frame body 14, the steering wheel is installed in the second lower frame body 13; the end of the second connecting beam 23 away from the optical axis 24 is fixed on the second lower frame body 13, the end of the optical axis 24 away from the second connecting beam 23 is fixed in the second lower frame body 13 of the adjacent vehicle frame 1; the driving assembly 42 is installed in the second upper frame body 14, and the carrying tray 41 is connected with the driving assembly 42 And pass through the upper end s
PUM
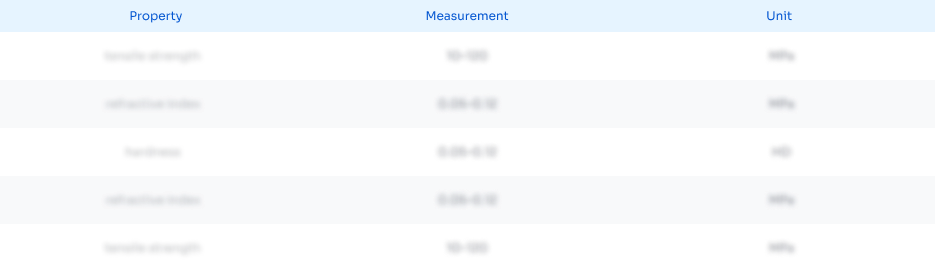
Abstract
Description
Claims
Application Information
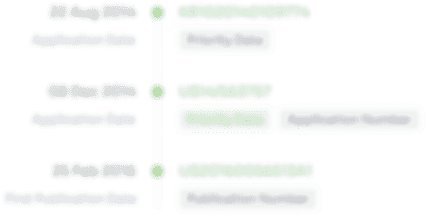
- R&D Engineer
- R&D Manager
- IP Professional
- Industry Leading Data Capabilities
- Powerful AI technology
- Patent DNA Extraction
Browse by: Latest US Patents, China's latest patents, Technical Efficacy Thesaurus, Application Domain, Technology Topic.
© 2024 PatSnap. All rights reserved.Legal|Privacy policy|Modern Slavery Act Transparency Statement|Sitemap