Multi-layer stacked composite material and preparation method and application thereof
A composite material and sheet technology, applied in chemical instruments and methods, application, lamination, etc., can solve the problems of high equipment cost, complex process, high energy consumption, etc., to improve barrier performance and shape memory performance, and improve comprehensive performance , The effect of simple processing technology
- Summary
- Abstract
- Description
- Claims
- Application Information
AI Technical Summary
Problems solved by technology
Method used
Image
Examples
Embodiment 1
[0033] In the present embodiment, the preparation method of 5 layers of PPC / modified thermoplastic starch (TPS) / CNC composite material is as follows:
[0034] Step (1), after taking by weighing 420g of dried cornstarch, 180g glycerol and 2.1g tartaric acid and stirring evenly, obtain modified TPS by granulating through a twin-screw extruder, wherein the rotating speed is 80r / min, and the feeding port of the extruder The heating temperature of each section of the machine head is: T1=90°C, T2=120°C, T3=130°C, T4=140°C, T5=145°C, T6=145°C, T7=140°C, T8=135°C.
[0035] Step (2), PPC (Henan Tianguan Group Co., Ltd., Mw=58700g / mol) weighs 450g, takes the modified TPS in step (1) and weighs 50g, and obtains PPC / modified TPS by water-cooling granulation through a twin-screw extruder. TPS composite material, wherein the rotation speed is 80r / min, the heating temperature of each section from the feed port to the head of the extruder is: T1=110°C, T2=120°C, T3=130°C, T4=135°C, T
Embodiment 2
[0041] In this example, the preparation method of 10 layers of PPC / modified TPS / CNC composite material is as follows:
[0042] Step (1), after taking by weighing 420g of dried cornstarch, 180g glycerol and 2.1g tartaric acid and stirring evenly, the modified TPS granulated by a twin-screw extruder, wherein the rotating speed is 80r / min, the feed port of the extruder The heating temperature of each section of the machine head is: T1=90°C, T2=120°C, T3=130°C, T4=140°C, T5=145°C, T6=145°C, T7=140°C, T8=135°C.
[0043] Step (2), PPC (Henan Tianguan Group Co., Ltd., Mw=58700g / mol) weighs 450g, takes the modified TPS in step (1) and weighs 50g, and obtains PPC / modified TPS by water-cooling granulation through a twin-screw extruder. TPS composite material, wherein the rotation speed is 80r / min, the heating temperature of each section from the feed port to the head of the extruder is: T1=110°C, T2=120°C, T3=130°C, T4=135°C, T5=140 °C, T6=140°C, T7=120°C, T8=120°C.
[0044]
Embodiment 3
[0048] In the present embodiment, the preparation method of 5 layers of PPC / modified TPS / CNC composite material is as follows:
[0049] Step (1), after taking by weighing 420g of dried cornstarch, 180g glycerol and 2.1g tartaric acid and stirring evenly, the modified TPS granulated by a twin-screw extruder, wherein the rotating speed is 80r / min, the feed port of the extruder The heating temperature of each section of the machine head is: T1=90°C, T2=120°C, T3=130°C, T4=140°C, T5=145°C, T6=145°C, T7=140°C, T8=135°C.
[0050] Step (2), get 44.5g dry PPC, modified TPS 5g and 0.5g CNC in step (1) to prepare PPC / modified TPS / CNC composite material by Haake torque rheometer, wherein heating temperature 130 ℃, rotor speed 60 rpm.
[0051] In step (3), the composite material in step (2) is molded into a plastic sheet by a flat vulcanizing machine, specifically preheated for 5 minutes, pressurized for 5 minutes, cooled for 3 minutes, the temperature is 130° C., and the pressure
PUM
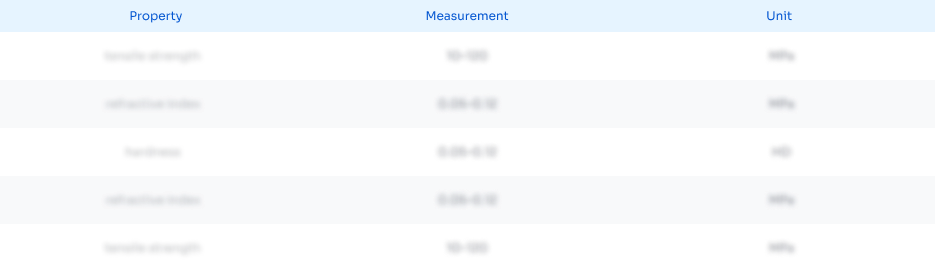
Abstract
Description
Claims
Application Information
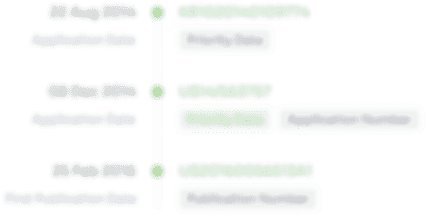
- R&D Engineer
- R&D Manager
- IP Professional
- Industry Leading Data Capabilities
- Powerful AI technology
- Patent DNA Extraction
Browse by: Latest US Patents, China's latest patents, Technical Efficacy Thesaurus, Application Domain, Technology Topic.
© 2024 PatSnap. All rights reserved.Legal|Privacy policy|Modern Slavery Act Transparency Statement|Sitemap