Preparation method of aminated graphene oxide
A technology of amination and graphene, which is applied in chemical instruments and methods, inorganic chemistry, carbon compounds, etc., can solve the problems of poor electrical conductivity and high temperature resistance, and achieve enhanced electrical conductivity and thermal stability, small sheet diameter, layered low number effect
- Summary
- Abstract
- Description
- Claims
- Application Information
AI Technical Summary
Problems solved by technology
Method used
Image
Examples
Example Embodiment
[0030] Example 1
[0031] Step 1, 50 kg of oxide oxide is uniformly dispersed in a 1000 kg solvent N, N-dimethylformamide (DMF), and sulfoxide, chlorinated submeiro is added to 1000 kg of solvent N, N-dimethylformamide (DMF), 5 ° C. The mass ratio of the sulfone to the oxide in graphene powder was 1: 4, and the reaction was heated to 60 ° C after the dropping was completed. The condensation reflux during the reaction was simultaneously absorbed. After 12h, the reaction was slowly added to the system. Gas produce, then filtrate, washed, to obtain activated acyl chloride oxide.
[0032] Step 2, 100 kg of polyphosphoric acid is added to the reaction kettle, heated to 160 ° C, then add 16.7 kg of nitrobenzoic acid and 12 kg of hydrochloride 12 kg, and immediately produce a large amount of gas, and stirring is uniform. The temperature was heated to 160 ° C for 2 h. The reaction liquid is cooled, and the polyphosphate is continuously hydrated in 600 kg of ice water, and the floccoli is pre
Example Embodiment
[0035] Example 2
[0036] Step 1, 50 kg of oxide oxide is uniformly dispersed in a 1000 kg solvent DMF by ultrasound, shearing, and emulsified composite diffracting, adding a chlorinated sulfoxide, and the mass ratio of the chloride and the oxide oxide in graphene powder. 1: 3, after the dropping is completed, the temperature is increased to 60 ° C for reaction, and the reflux during the reaction, the exhaust gas absorption is simultaneously absorbed. After 10 h, the appropriate amount of water is slowly added to the system without gas production, then filtrate, wash, and activate Chloride oxide.
[0037] Step 2, 100 kg of polyphosphoric acid is added to the reactor, heated to 150 ° C, then adding 16.7 kg of nitrobenzoic acid and 12 kg of hydrochloride 12kg, immediately producing a large amount of gas, agitating vigorously mixed mixing. The temperature was raised to 150 ° C for 5 h. The reaction liquid is cooled, and the polyphosphate is continuously hydrated in 600 kg of ice water,
Example Embodiment
[0042] Example 3
[0043] Step 1, 50 kg of oxide oxide is uniformly dispersed in a 1000 kg solvent DMF by ultrasound, shearing, and emulsified composite diffracting, adding a chlorinated sulfoxide, and the mass ratio of the chloride and the oxide oxide in graphene powder. 1: 3, after the dropping is completed, the temperature is increased to 60 ° C for reaction, and the reflux during the reaction, the exhaust gas absorption is simultaneously absorbed. After 10 h, the appropriate amount of water is slowly added to the system without gas production, then filtrate, wash, and activate Chloride oxide.
[0044] Step 2, 100 kg of polyphosphoric acid is added to the reaction kettle, heated to 160 ° C, then add 16.7 kg of nitrobenzoic acid and 12 kg of hydrochloride 12 kg, and immediately produce a large amount of gas, and stirring is uniform. The temperature was raised to 150 ° C for 5 h. The reaction liquid is cooled, and the polyphosphate is continuously hydrated in 600 kg of ice water, pr
PUM
Property | Measurement | Unit |
---|---|---|
Film diameter | aaaaa | aaaaa |
Thickness | aaaaa | aaaaa |
Abstract
Description
Claims
Application Information
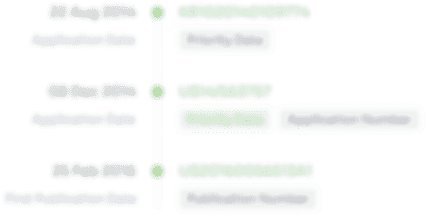
- R&D Engineer
- R&D Manager
- IP Professional
- Industry Leading Data Capabilities
- Powerful AI technology
- Patent DNA Extraction
Browse by: Latest US Patents, China's latest patents, Technical Efficacy Thesaurus, Application Domain, Technology Topic.
© 2024 PatSnap. All rights reserved.Legal|Privacy policy|Modern Slavery Act Transparency Statement|Sitemap