Mullite-based ceramic material and preparation method thereof
A ceramic material, mullite-based technology, applied in the field of refractory ceramic materials, can solve problems such as poor dispersion uniformity, difficult whisker dispersion, and difficult production, to achieve high whisker content, reduce calcination time, and reduce sintering time Effect
- Summary
- Abstract
- Description
- Claims
- Application Information
AI Technical Summary
Problems solved by technology
Method used
Examples
Example Embodiment
[0030] Example 1
[0031] Preparation of mullite seeds, including the following steps:
[0032] According to the ratio of orthosilicate, aluminum nitrate and ethanol of 3 mol: 2 mol: 1 L, 0.3 mol orthosilicate and 0.2 mol of nitrate were mixed and added to 100 ml of ethanol, and 1 mol / L was added dropwise. The hydrochloric acid solution to a pH of 2, reacted at 60 ° C for 3 h, resulting in silicon aluminum-soluble, add 4 mol / L of ammonia water to a silicon aluminum aluminum, reacting 10 h at 60 ° C, resulting silicon Aluminum gel, after drying the silica gel at 70 ° C, calcined at 1000 ° C, cooling, and the diameter of 52-55 nm was obtained, and the length of 1.5-1.7 μm was produced.
[0033] Preparation of phosphate binders, including the following steps:
[0034] Step A1, will Al (OH) 3 Join the mass fraction of H 3 PO 4 Al (OH) 3 With h 3 PO 4 The molar ratio of the solute in the solution was 5: 4 to obtain a mixed liquid, and the mixture was warmed to 85 ° C and stirred f
Example Embodiment
[0041] Example 2
[0042] Preparation of mullite seeds, including the following steps:
[0043] According to the ratio of orthosilicate, aluminum nitrate and ethanol of 3 mol: 2 mol: 1 L, 0.3 mol orthosilicate and 0.2 mol of nitrate were mixed and added to 100 ml of ethanol, and 1 mol / L was added dropwise. The hydrochloric acid solution is 2, reacted at 60 ° C for 4 h, resulting in silicon aluminum-soluil, add 4 mol / L of ammonia water to a silica aluminumol, reacts 11h at 60 ° C, resulting silicon Aluminum gel, after drying the silica gel at 80 ° C, calcined at 1200 ° C, cooled, and the diameter of 58-63 nm was produced, the length of 1.6-1.8 μm was produced.
[0044] Preparation of phosphate binders, including the following steps:
[0045] Step A1, will Al (OH) 3 Join the mass fraction of H 3 PO 4 Al (OH) 3 With h 3 PO 4 The molar ratio of the solute in the solution was 5: 4 to obtain a mixed liquid, and the mixture was warmed to 85 ° C and stirred for 3 h, resulting in a vi
Example Embodiment
[0052] Example 3
[0053] Preparation of mullite seeds, including the following steps:
[0054] According to the ratio of orthosilicate, aluminum nitrate and ethanol of 3 mol: 2 mol: 1 L, 0.3 mol orthosilicate and 0.2 mol of nitrate were mixed and added to 100 ml of ethanol, and 1 mol / L was added dropwise. The hydrochloric acid solution is 2, reacted at 60 ° C for 5 h, and a silicon aluminum-soluble is obtained, and 4 mol / L is added to the silicone aluminum sol. Aluminum gel, after drying the silica gel at 90 ° C, calcined at 1300 ° C, and then cooled, the diameter of 62-69 nm, the length of 1.7-2.0 μm was produced.
[0055] Preparation of phosphate binders, including the following steps:
[0056] Step A1, will Al (OH) 3 Join the mass fraction of H 3 PO 4 Al (OH) 3 With h 3 PO 4 The molar ratio of the solute in the solution was 5: 4, resulting in a mixture, and the mixture was warmed to 85 ° C and stirred for 4 h, resulting in a viscous liquid;
[0057] Step A2, according to
PUM
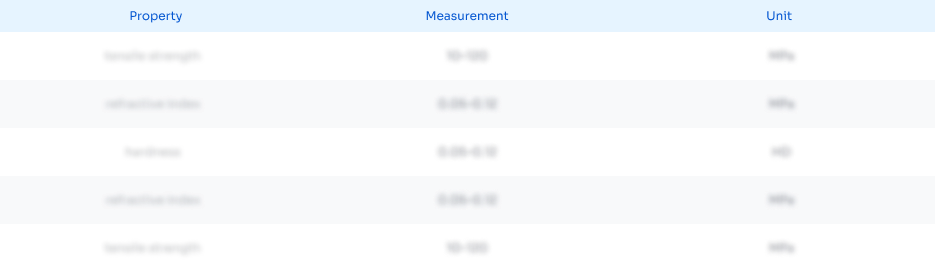
Abstract
Description
Claims
Application Information
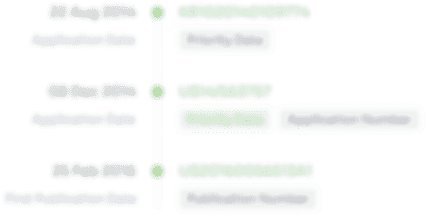
- R&D Engineer
- R&D Manager
- IP Professional
- Industry Leading Data Capabilities
- Powerful AI technology
- Patent DNA Extraction
Browse by: Latest US Patents, China's latest patents, Technical Efficacy Thesaurus, Application Domain, Technology Topic.
© 2024 PatSnap. All rights reserved.Legal|Privacy policy|Modern Slavery Act Transparency Statement|Sitemap