Inorganic-organic coating composite material for nodular cast iron pipe and preparation method of inorganic-organic coating composite material
A ductile iron pipe, organic coating technology, applied in coatings, anti-corrosion coatings, fire-resistant coatings, etc., can solve the problems of fragile protective film, uniform adhesion, poor corrosion resistance, etc., to enhance comprehensive mechanical properties and water resistance. Corrosion resistance and other properties, increase high temperature resistance and corrosion resistance, the effect of simple methods
- Summary
- Abstract
- Description
- Claims
- Application Information
AI Technical Summary
Benefits of technology
Problems solved by technology
Method used
Examples
preparation example Construction
[0028] According to the ductile iron pipe inorganic-organic coating composite material and the preparation method thereof according to the embodiment of the present invention, before preparing the inorganic-organic coating composite material, the surface of the ductile iron pipe is subjected to shot blasting, degreasing, chemical cleaning, and water washing. One or more pretreatments, for example, the surface pretreatment of the ductile iron pipe may include: shot blasting the surface of the ductile iron pipe, degreasing and derusting the outer surface of the pipe to Sa2.5 level, and then using acetone, alkali and / or Wash with acid and deionized water, and dry; after sufficient pretreatment, the bonding force between the coating and the substrate can be enhanced, making the coating more firm.
[0029] The present invention will be further described below in conjunction with more specific examples:
Embodiment 1
[0031] (1) Surface pretreatment of ductile iron pipes
[0032] The surface of the ductile iron pipe is shot blasted, and the outer surface of the pipe is degreased and derusted to Sa2.5 level, and then cleaned with acetone, alkali, pickling, and deionized water, and then dried.
[0033] (2) Nano inorganic metal oxide coating
[0034] The nano-zirconia sol was prepared by the sol-gel method, and the pretreated ductile iron pipe was immersed in the nano-zirconia sol by the dipping and pulling method. The immersion and lifting speed was 3mm / s, and the soaking time was 3min. Let dry for 30 minutes. Deposit two layers of nano-zirconia coatings according to the above deposition process, and heat-treat the samples in an environment of 240°C for 60 minutes to remove excess organic matter in the coatings.
[0035] (3) Montmorillonite modified polysiloxane coating
[0036] Add silica sol into the reactor, and add acetic acid-ammonium acetate composite catalyst at the same time, the ma
Embodiment 2
[0041] (1) Surface pretreatment of ductile iron pipes
[0042] The surface of the ductile iron pipe is shot blasted, and the outer surface of the pipe is degreased and derusted to Sa2.5 level, and then cleaned with acetone, alkali, pickling, and deionized water, and then dried.
[0043] (2) Nano inorganic metal oxide coating
[0044] The nano-silica sol was prepared by the sol-gel method, and the pretreated ductile iron pipe was immersed in the nano-silica sol by the dipping and pulling method. The immersion and lifting speed was 3mm / s, and the soaking time was 3min. Let dry for 30 minutes. Two layers of nano-silica coatings were deposited according to the above deposition process, and the samples were heat-treated in an environment of 240° C. for 60 minutes to remove excess organic matter in the coatings.
[0045] (3) Montmorillonite modified polysiloxane coating
[0046] Add silica sol into the reactor, and add acetic acid-ammonium acetate composite catalyst at the same ti
PUM
Property | Measurement | Unit |
---|---|---|
Hardness | aaaaa | aaaaa |
Adhesion | aaaaa | aaaaa |
Adhesion | aaaaa | aaaaa |
Abstract
Description
Claims
Application Information
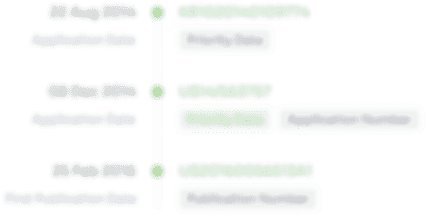
- R&D Engineer
- R&D Manager
- IP Professional
- Industry Leading Data Capabilities
- Powerful AI technology
- Patent DNA Extraction
Browse by: Latest US Patents, China's latest patents, Technical Efficacy Thesaurus, Application Domain, Technology Topic.
© 2024 PatSnap. All rights reserved.Legal|Privacy policy|Modern Slavery Act Transparency Statement|Sitemap