Toughening equipment for polyester resin
A polyester resin and toughening technology, applied in the field of polyester resin, can solve the problems of unfavorable dispersion of the second phase material, affecting the toughening effect of polyester resin, difficult to rotate and mix, etc., to achieve toughening effect, facilitate dispersion, The effect of internal fluid uniformity
- Summary
- Abstract
- Description
- Claims
- Application Information
AI Technical Summary
Benefits of technology
Problems solved by technology
Method used
Image
Examples
Embodiment Construction
[0024] The following will clearly and completely describe the technical solutions in the embodiments of the present invention with reference to the accompanying drawings in the embodiments of the present invention. Obviously, the described embodiments are only some, not all, embodiments of the present invention.
[0025] see Figure 1-5, an embodiment provided by the present invention: a kind of toughening equipment for polyester resin, including a protective shell 1, the cross direction of the outer side of the protective shell 1 is welded with supporting legs 2, and the middle of the upper end of the protective shell 1 is installed with a Liquid pipe 6, the lower end of the outer side of the protective shell 1 is equipped with a liquid discharge pipe 4, the middle of the lower end of the protective shell 1 is installed with a first drive motor 3, the inside of the protective shell 1 is provided with a mixing chamber 16, a liquid inlet pipe 6 and a liquid discharge pipe 4 commun
PUM
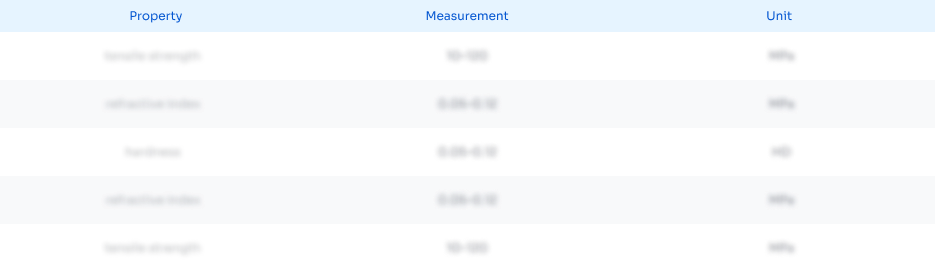
Abstract
Description
Claims
Application Information
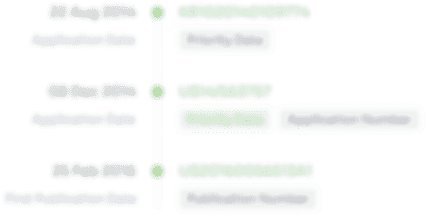
- R&D Engineer
- R&D Manager
- IP Professional
- Industry Leading Data Capabilities
- Powerful AI technology
- Patent DNA Extraction
Browse by: Latest US Patents, China's latest patents, Technical Efficacy Thesaurus, Application Domain, Technology Topic.
© 2024 PatSnap. All rights reserved.Legal|Privacy policy|Modern Slavery Act Transparency Statement|Sitemap