Tear-resistant blown film and preparation process thereof
A technology for blown film and preparation process, applied in the field of packaging bags, can solve problems such as deformation and damage, affecting the normal use of film bags, etc., and achieve the effects of improving service life, increasing roughness, and improving tensile strength
- Summary
- Abstract
- Description
- Claims
- Application Information
AI Technical Summary
Benefits of technology
Problems solved by technology
Method used
Image
Examples
Embodiment 2
[0052] like Figure 4 to Figure 7 As shown, a preparation process of a tear-resistant blown film is used to prepare the tear-resistant film in Example 1, and the preparation steps include:
[0053] S1 material preparation, configure the master batch raw materials of inner layer 2 and outer layer 3 respectively according to the proportioning, wherein the master batch raw materials of outer layer 3 include:
[0054] HDPE 80%;
[0055] Antioxidant 1%;
[0056] UV Absorber 1%
[0057] Toughening agent 5%;
[0058] The masterbatch raw materials for inner layer 2 include:
[0059] Low density polyethylene 65%;
[0060] Linear low density polyethylene 25%;
[0061] Couplant 5%;
[0062] staple fiber mixture 5%;
[0063] S2 mix materials, put the master batch materials of outer layer 3 and inner layer 2 into two screw extruders respectively for melt extrusion to obtain blow molding materials in molten state, and set the melting temperature of the two screw extruders 105-115℃ and
Embodiment 3
[0067] like Figure 4 to Figure 7 As shown, a preparation process of a tear-resistant blown film is used to prepare the tear-resistant film in Example 1, and the preparation steps include:
[0068] S1 material preparation, configure the master batch raw materials of inner layer 2 and outer layer 3 respectively according to the proportioning, wherein the master batch raw materials of outer layer 3 include:
[0069] HDPE 91%;
[0070] Antioxidant 1%;
[0071] UV Absorber 2%
[0072] Toughening agent 5%;
[0073] The masterbatch raw materials for inner layer 2 include:
[0074] Low density polyethylene 70%;
[0075] Linear low density polyethylene 10%;
[0076] Couplant 8%;
[0077] Short fiber mixture 2%;
[0078] S2 mix materials, put the master batch materials of outer layer 3 and inner layer 2 into two screw extruders respectively for melt extrusion to obtain blow molding materials in molten state, and set the melting temperature of the two screw extruders 105-115℃ and
PUM
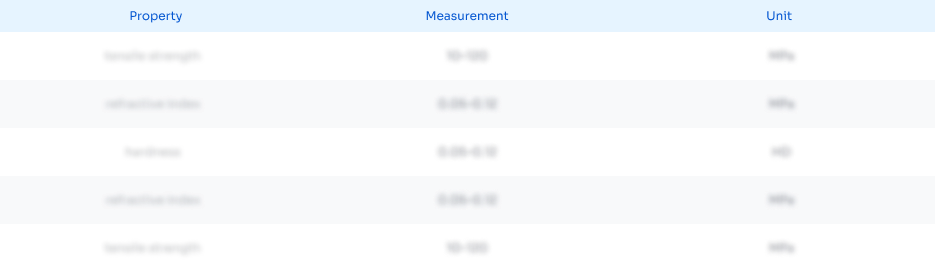
Abstract
Description
Claims
Application Information
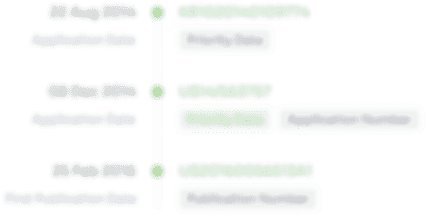
- R&D Engineer
- R&D Manager
- IP Professional
- Industry Leading Data Capabilities
- Powerful AI technology
- Patent DNA Extraction
Browse by: Latest US Patents, China's latest patents, Technical Efficacy Thesaurus, Application Domain, Technology Topic.
© 2024 PatSnap. All rights reserved.Legal|Privacy policy|Modern Slavery Act Transparency Statement|Sitemap