Amorphous alloy with increased operating induction
An amorphous and metal alloy technology, which is used in the manufacture of inductors/transformers/magnets, circuits, magnetic objects, etc., can solve the problem that amorphous metal alloys cannot obtain ideal excitation power, etc., to reduce core loss and reduce iron. Core size, effect of reducing heat loss
- Summary
- Abstract
- Description
- Claims
- Application Information
AI Technical Summary
Problems solved by technology
Method used
Examples
example 1
[0044] With chemical composition as Fe 80 B 11 Si 9 The 6.7” wide METGLAS Alloy SA-1 was fabricated into sixteen single-phase winding magnetic cores for commercial distribution transformers. Each iron core weighs about 75kg. The sixteen iron cores were divided into four groups, and each group was annealed at 355°C according to different soaking times. The baseline anneal soak time to achieve minimum core loss is approximately 20 minutes. The other three groups were annealed according to the soaking time of 30, 40 and 60 min, increasing the soaking time by 50%, 100% and 150%, respectively. exist Figure 5 and 6 The results obtained for all these cores are shown in . Each time the soaking time was increased, the excitation power decreased significantly. It was also found that prolonging the soaking time can reduce the excitation power.
example 2
[0046] With chemical composition as Fe 80 B 11 Si 9 The 6.7” wide METGLAS Alloy SA-1 is made into three single-phase winding magnetic cores for commercial distribution transformers. Each core weighs approximately 118kg and care is taken to minimize thermal gradient effects during heating and cooling. The cores were annealed with a soak time of 20 minutes, using a peak temperature of about 370°C instead of the usual 355°C. The excitation power and core loss obtained by measuring these high-temperature annealed iron cores were compared with Figure 2a and 2b The iron core annealed according to the conventional method is compared. It can be seen that if the peak temperature used in the core annealing process is increased, the excitation power will be significantly reduced, while the core loss is only slightly increased. The result achieved by increasing the annealing peak temperature in Example 2 is similar to the effect produced by prolonging the annealing soak time in ...
example 3
[0048] With chemical composition as Fe 80 B 11 Si 9 The 6.7” wide METGLAS Alloy SA-1 made straight laboratory sampling. Linear samples were subjected to 2-hour isochronal annealing at various temperatures in a magnetic field environment. The excitation power and core loss obtained by measuring these straight laboratory samples are expressed as a function of temperature in Figs. 1a and 1b. It can be seen that if the annealing peak temperature is increased by at least 5°C, the excitation power will drop significantly.
PUM
Property | Measurement | Unit |
---|---|---|
mass | aaaaa | aaaaa |
Abstract
Description
Claims
Application Information
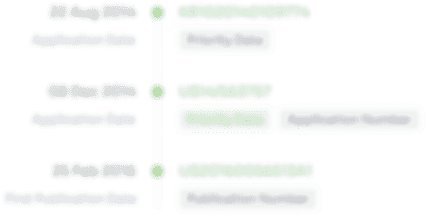
- R&D Engineer
- R&D Manager
- IP Professional
- Industry Leading Data Capabilities
- Powerful AI technology
- Patent DNA Extraction
Browse by: Latest US Patents, China's latest patents, Technical Efficacy Thesaurus, Application Domain, Technology Topic.
© 2024 PatSnap. All rights reserved.Legal|Privacy policy|Modern Slavery Act Transparency Statement|Sitemap