Polymer resin composition, related method for forming a pattern, and related method for fabricating a capacitor
a technology of polymer resin and composition, which is applied in the field of polymer resin composition, can solve the problems of difficult to deposit the oxide used as a blocking layer without forming a void, the manufacturing productivity may be relatively low, and the number of shots in the exposure process may be reduced, and the process time may be reduced. , the effect of improving the productivity of the semiconductor device manufacturing process
- Summary
- Abstract
- Description
- Claims
- Application Information
AI Technical Summary
Benefits of technology
Problems solved by technology
Method used
Image
Examples
synthesis example 1
[0158]In Synthesis Example 1, about 501.4 g of propyleneglycol monomethylether acetate (Shiny Company, Taiwan) was added as a solvent to a 1,000 mL flask coupled to a reflux condenser and a stirrer. The solvent was stirred and a temperature of the solvent was increased up to about 80° C. A reaction temperature was kept at a temperature of about 80° C., and a mixture of about 152 g of benzyl methacrylate (Aldrich, U.S.A.), about 43.7 g of 2-hydroxyethyl acrylate (Aldrich, U.S.A.), about 22.96 g of methacrylic acid (Aldrich, U.S.A.), and about 40.5 g of dimethyl-2,2′-azobis(2-methylpropionate) (V-601, Wako Corp., Japan) was dropped into the flask for one to three hours. After all of the mixture was dropped into the flask, the reaction temperature was kept at a temperature of about 80° C. A mixture in the flask was stirred and reacted for about four to five hours, and thus a transparent copolymer was produced. Characteristics of the copolymer were measured using a gel permeation chromatog
synthesis example 2
[0159]In Synthesis Example 2, the copolymer was synthesized through substantially the same processes as those used to synthesize Synthesis Example 1, except that the mixture dropped into the flask was a mixture of about 150.9 g of benzyl methacrylate, about 43.7 g of 2-hydroxyethyl acrylate, about 24.1 g of methacrylic acid, and about 40.5 g of dimethyl-2,2′-azobis(2-methylpropionate). Characteristics of the copolymer were measured using a gel permeation chromatography. The copolymer that was produced had about 7,000 of a weight average molecular weight based on a polystyrene standard, about 2,900 of a number average molecular weight based on a polystyrene standard, and about 29.01 percent by weight of solid content measured after drying the copolymer at a temperature of about 160° C. for about one hour. Also, the copolymer that was produced had about 11 percent by weight of methacrylic acid.
synthesis example 3
[0160]In Synthesis Example 3, the copolymer was synthesized through substantially the same processes as those used to synthesize Synthesis Example 1, except that the mixture dropped into the flask was a mixture of about 149.8 g of benzyl methacrylate, about 43.7 g of 2-hydroxyethyl acrylate, about 25.1 g of methacrylic acid, about 25.15 g of alpha-methylstyrene dimer, and about 40.5 g of dimethyl-2,2′-azobis(2-methylpropionate). Characteristics of the copolymer were measured using gel permeation chromatography. The copolymer that was produced had about 7,000 of a weight average molecular weight based on a polystyrene standard, about 2,900 of a number average molecular weight based on a polystyrene standard, and about 28.67 percent by weight of a solid content measured after drying the copolymer at a temperature of about 160° C. for about one hour. Also, the copolymer that was produced had about 11.5 percent by weight of methacrylic acid.
Preparation of a Polymer Resin Composition
PUM
Property | Measurement | Unit |
---|---|---|
Temperature | aaaaa | aaaaa |
Temperature | aaaaa | aaaaa |
Percent by mass | aaaaa | aaaaa |
Abstract
Description
Claims
Application Information
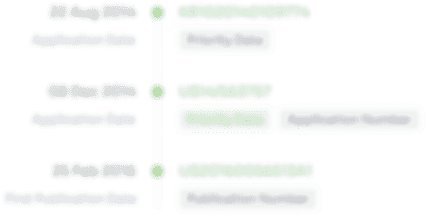
- R&D Engineer
- R&D Manager
- IP Professional
- Industry Leading Data Capabilities
- Powerful AI technology
- Patent DNA Extraction
Browse by: Latest US Patents, China's latest patents, Technical Efficacy Thesaurus, Application Domain, Technology Topic.
© 2024 PatSnap. All rights reserved.Legal|Privacy policy|Modern Slavery Act Transparency Statement|Sitemap