Solid type rubber-based pressure-sensitive adhesive composition and pressure-sensitive adhesive sheet thereof
- Summary
- Abstract
- Description
- Claims
- Application Information
AI Technical Summary
Benefits of technology
Problems solved by technology
Method used
Examples
example 1
[0043]Into a 3-liter pressure kneader heated at 150° C., 1,500 g of an acrylic rubber (Mooney viscosity (ML1+4, 100° C.):30) including a copolymer of 95 parts of butyl acrylate and 5 parts of acrylic acid was introduced, and kneaded for 2 minutes. Then, 750 g of a terpene-phenol resin (“Mighty Ace G125” manufactured by Yasuhara Chemical Co., Ltd.) was introduced in several batches thereinto as a tackifier, followed by kneading for about 15 minutes. Further, 300 g of a polyether ester (“ADK CIZER RG735” manufactured by ADEKA Co., Ltd.) was introduced in several batches thereinto as a softener, followed by kneading for about 15 minutes.
[0044]Finally, 30 g of an isocyanate-based crosslinking agent (“Coronate HX manufactured by Nippon Polyurethane Industry Co., Ltd.) was introduced thereinto as a crosslinking agent, followed by kneading for about 5 minutes. Then, the resulting product was taken out of the kneader to prepare a solid type rubber-based pressure-sensitive adhesive composition.
example 2
[0051]Into a 3-liter pressure kneader heated at 130° C., 1,500 g of an acrylic rubber (Mooney viscosity (ML1+4, 100° C.):30) including a copolymer of 70 parts of butyl acrylate, 30 parts of ethyl acrylate and 5 parts of hydroxyethyl acrylate was introduced, and kneaded for 2 minutes. Then, 750 g of a terpene-phenol resin (“Mighty Ace K125” manufactured by Yasuhara Chemical Co., Ltd.) was introduced in several batches thereinto as a tackifier, followed by kneading for about 10 minutes. Further, 300 g of an acrylic polymer tackifier (“Arufon UP1000” manufactured by Toagosei Co., Ltd.) was introduced in several batches thereinto as a softener, followed by kneading for about 10 minutes.
[0052]Finally, 30 g of an isocyanate-based crosslinking agent (“Coronate HX manufactured by Nippon Polyurethane Industry Co., Ltd.) was introduced thereinto as a crosslinking agent, followed by kneading for about 2 minutes. Then, the resulting product was taken out of the kneader to prepare a solid type rubb
example 3
[0055]Into a 3-liter pressure kneader heated at 130° C., 1,500 g of an acrylic rubber (Mooney viscosity (ML1+4, 100° C.):30) including a copolymer of 95 parts of butyl acrylate and 5 parts of hydroxyethyl acrylate was introduced, and kneaded for 2 minutes. Then, 750 g of a terpene-phenol resin (“YP90L” manufactured by Yasuhara Chemical Co., Ltd.) was introduced in several batches thereinto as a tackifier, followed by kneading for about 10 minutes. Further, 150 g of a polyether ester (“ADK CIZER RG735” manufactured by ADEKA Co., Ltd.) was introduced in several batches thereinto as a softener, followed by kneading for about 10 minutes.
[0056]Finally, 7.5 g of an isocyanate-based crosslinking agent (“Coronate HX manufactured by Nippon Polyurethane Industry Co., Ltd.) was introduced thereinto as a crosslinking agent, followed by kneading for about 2 minutes. Then, the resulting product was taken out of the kneader to prepare a solid type rubber-based pressure-sensitive adhesive composition.
PUM
Property | Measurement | Unit |
---|---|---|
Percent by mass | aaaaa | aaaaa |
Percent by mass | aaaaa | aaaaa |
Percent by mass | aaaaa | aaaaa |
Abstract
Description
Claims
Application Information
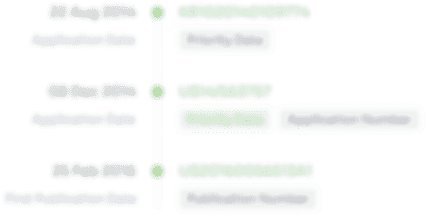
- R&D Engineer
- R&D Manager
- IP Professional
- Industry Leading Data Capabilities
- Powerful AI technology
- Patent DNA Extraction
Browse by: Latest US Patents, China's latest patents, Technical Efficacy Thesaurus, Application Domain, Technology Topic.
© 2024 PatSnap. All rights reserved.Legal|Privacy policy|Modern Slavery Act Transparency Statement|Sitemap