Extruder screw for a multi-screw extruder for plastics extrusion
a multi-screw, extruder technology, applied in the direction of mixing, transportation and packaging, rotary stirring mixers, etc., can solve the problems of insufficient solids melting, accelerated plastic hydrolysis degradation, and disassembly and assembly of screw heads, so as to reduce the residence time, the torque to be transmitted is significantly higher, and the drive power is higher
- Summary
- Abstract
- Description
- Claims
- Application Information
AI Technical Summary
Benefits of technology
Problems solved by technology
Method used
Examples
Embodiment Construction
[0026]FIG. 1 shows a section of an extruder screw 100 in perspective view, as far as essential for the invention. Plastic particles or plastic melt, respectively, are drawn in from the right in the position shown in FIG. 1 and discharged to the left.
[0027]Four function zones are provided across the length:[0028]A first longitudinal section after the intake, not visible here, forms the so-called metering zone 1, in which the plastic granulate is melted and homogenized.[0029]A degassing zone 2 follows. A suction device is provided on the extruder housing, which is also not shown here, so that volatile components can be extracted from the degassing zone 2.[0030]The melt melted in metering zone 1 and degassed in the subsequent degassing zone 2 must pass through a drive zone 3 and is compressed and discharged in a compression and / or discharge zone 4 behind it.
[0031]From a design point of view, the extruder screw 100 is essentially divided into three sections:[0032]a first mono-screw sect...
PUM
Property | Measurement | Unit |
---|---|---|
volumes | aaaaa | aaaaa |
surface area | aaaaa | aaaaa |
compression | aaaaa | aaaaa |
Abstract
Description
Claims
Application Information
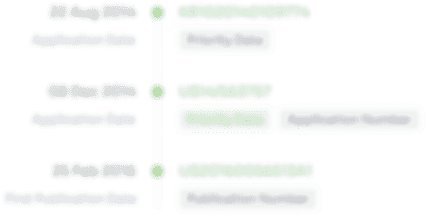
- R&D Engineer
- R&D Manager
- IP Professional
- Industry Leading Data Capabilities
- Powerful AI technology
- Patent DNA Extraction
Browse by: Latest US Patents, China's latest patents, Technical Efficacy Thesaurus, Application Domain, Technology Topic.
© 2024 PatSnap. All rights reserved.Legal|Privacy policy|Modern Slavery Act Transparency Statement|Sitemap