Composite core for the casting of engine head decks
a technology of engine head deck and composite core, which is applied in the direction of manufacturing tools, foundry patterns, moulding apparatus, etc., can solve the problems of failure to meet the more strict emission requirements of today, the cylinder bore surface of such engine blocks is too susceptible to wear, and the construction is considered too heavy, so as to reduce thermal hot spots and bore wall distortion, and the cooling of the cylinder wall is better and more uniform.
- Summary
- Abstract
- Description
- Claims
- Application Information
AI Technical Summary
Benefits of technology
Problems solved by technology
Method used
Image
Examples
Embodiment Construction
[0028]FIG. 1 demonstrates a closed deck engine block 2 for use in a high pressure die cast engine block assembly in accordance with the present invention. The engine block is high pressure die cast, preferably in accordance with the method for casting an engine block assembly having at least one cast in place cylinder bore in the engine block and a closed head deck surface described herein.
[0029]As shown in FIG. 1, the closed deck engine block 2 includes at least two cylinder bores 4 in the engine block. The cylinder bores may be cast in place and include a top surface 6 and an outer surface 8. As shown in FIGS. 3 and 4, the outer surface 8 further includes an upper outer surface 10 and a lower outer surface 12. The lower outer surface 12 of the cylinder bores 4 may further define at least one surface area 14 for interfacing with the engine block during casting to cast the at least two cylinder bores 4 in place in the engine block 2.
[0030]Referring now to FIGS. 1 and 2, the closed deck
PUM
Property | Measurement | Unit |
---|---|---|
Pressure | aaaaa | aaaaa |
Area | aaaaa | aaaaa |
Melting point | aaaaa | aaaaa |
Abstract
Description
Claims
Application Information
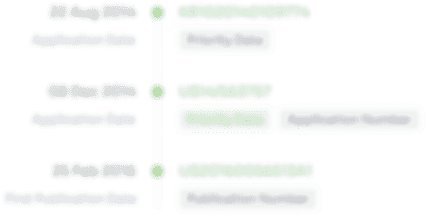
- R&D Engineer
- R&D Manager
- IP Professional
- Industry Leading Data Capabilities
- Powerful AI technology
- Patent DNA Extraction
Browse by: Latest US Patents, China's latest patents, Technical Efficacy Thesaurus, Application Domain, Technology Topic.
© 2024 PatSnap. All rights reserved.Legal|Privacy policy|Modern Slavery Act Transparency Statement|Sitemap