Die-casting mould casting method and flow gate of die-casting mould
A die-casting mold and inner gate technology, which is applied in the field of metal die-casting, can solve the problems of slow heat dissipation and solidification of molten metal in castings, reduced gate speed, and low yield, so as to achieve compact structure, increase yield, and high yield Effect
- Summary
- Abstract
- Description
- Claims
- Application Information
AI Technical Summary
Benefits of technology
Problems solved by technology
Method used
Image
Examples
Embodiment Construction
[0013] The present invention will be further described below in conjunction with the accompanying drawings and specific embodiments.
[0014] A die-casting mold casting method, the flow velocity of the punch in the die-casting process is 0.4 m / s to 0.8 m / s (0.6 m / s in this example, it can also be 0.4 m / s, 0.5 m / s, 0.7 m / s or 0.8.7 m / s, etc.), and the cross-section of the ingate 1 is a polygonal structure, and the rest are the same as those of the prior art.
[0015] Such as figure 1 and figure 2 As shown, the cross section of the ingate 1 includes a first straight side 2, a second straight side 3, a third straight side 4, a fourth straight side 5, a first hypotenuse 6 and a second hypotenuse 7, The first straight side 2 is parallel to the third straight side 4, the second straight side 3 is parallel to the fourth straight side 5, and the distance between the first straight side 2 and the third straight side 4 is equal to the second straight side 3 and the fourth
PUM
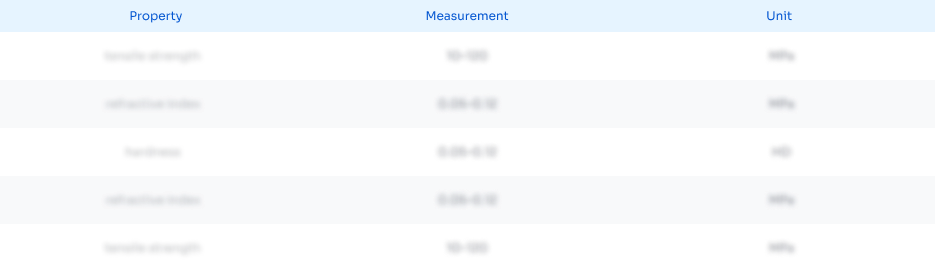
Abstract
Description
Claims
Application Information
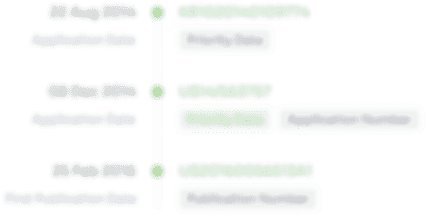
- R&D Engineer
- R&D Manager
- IP Professional
- Industry Leading Data Capabilities
- Powerful AI technology
- Patent DNA Extraction
Browse by: Latest US Patents, China's latest patents, Technical Efficacy Thesaurus, Application Domain, Technology Topic.
© 2024 PatSnap. All rights reserved.Legal|Privacy policy|Modern Slavery Act Transparency Statement|Sitemap