Metal-ceramic composite fibrous membrane tube and preparation method thereof
A ceramic composite and fiber membrane technology, which is applied in the field of fiber membrane tubes, can solve problems such as difficult assembly, unsuitability for high temperature, and difficulty in forming and sintering metal membrane tubes, so as to achieve wide application fields, increase transmission rate or thermal Exchange performance, effect of small diameter
- Summary
- Abstract
- Description
- Claims
- Application Information
AI Technical Summary
Benefits of technology
Problems solved by technology
Method used
Image
Examples
Embodiment 1
[0017] Example 1: Preparation and use of stainless steel-alumina composite porous fiber membrane tube
[0018] Weigh 0.4g of polyvinylpyrrolidone (PVP), 1.84g of polyethersulfone (PESf), 9.2g of N-methyl-1-pyrrolidone (NMP), 97.68g of stainless steel powder with a particle size of 1 to 10 μm, and 10.86g of stainless steel powder with a particle size of 1 μm. Alumina powder, mixed with QM-3SP2 planetary ball mill manufactured by Nanjing University Instrument Factory, and ball milled at 20Hz for 48 hours to obtain a uniform slurry that can just flow out of the spinneret without pressure.
[0019] attached figure 1 A schematic diagram of the green body forming process in the preparation method of the metal-ceramic composite fiber membrane tube of the present invention is given. like figure 1 As shown in , the outlet of the spinneret with the interlayer gap of 0.5mm and the outer diameter of the inner tube is 1.16mm composed of two concentric circular tubes with flush lower end sur
Embodiment 2
[0032] Example 2: Preparation and use of stainless steel-alumina composite dense fiber membrane tube
[0033] The stainless steel-alumina composite fiber membrane tube body was prepared by the same method as in Example 1, except that the sintering temperature was increased to 1400°C, and the stainless steel-alumina composite dense fiber membrane tube could be obtained. The stainless steel-alumina composite dense membrane tube can be used for fluid heat exchange due to its good thermal conductivity and considerable specific surface area.
Embodiment 3
[0034] Example 3: Assembly and use of stainless steel-alumina composite fiber membrane tube
[0035] First prepare a stainless steel-alumina composite fiber membrane tube by the same method as in Example 1; then take a bundle of membrane tubes, and weld the parts near the two ends to two identical disc-shaped meshes with mesh apertures slightly larger than the fiber membrane tubes. plate, or directly weld the parts near both ends of the membrane tube on a plane perpendicular to the membrane tube to obtain a tube bundle of the composite fiber membrane tube.
[0036] The tube bundle made of the porous composite fiber membrane tube prepared by the invention can be used as a filter element.
[0037] A typical application is: the sieve plate is welded on the stainless steel sleeve, and the stainless steel sleeve is filled with impurity-containing water to be treated under pressure, then the membrane tube can flow out the water that has been filtered out of some impurities and microorg
PUM
Property | Measurement | Unit |
---|---|---|
Outer diameter | aaaaa | aaaaa |
Tube wall thickness | aaaaa | aaaaa |
The inside diameter of | aaaaa | aaaaa |
Abstract
Description
Claims
Application Information
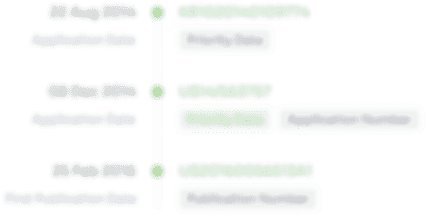
- R&D Engineer
- R&D Manager
- IP Professional
- Industry Leading Data Capabilities
- Powerful AI technology
- Patent DNA Extraction
Browse by: Latest US Patents, China's latest patents, Technical Efficacy Thesaurus, Application Domain, Technology Topic.
© 2024 PatSnap. All rights reserved.Legal|Privacy policy|Modern Slavery Act Transparency Statement|Sitemap