Electrostatic spinning film and preparation method and application thereof
A technology of electrospinning and hexafluoroisopropanol, which is applied in the direction of electrospinning, spinning solution preparation, textiles and papermaking, etc., and achieves the effects of simple preparation method, controllable process and various types
- Summary
- Abstract
- Description
- Claims
- Application Information
AI Technical Summary
Problems solved by technology
Method used
Image
Examples
Embodiment 1
[0048] In this embodiment, the haze protective electrospun membrane is prepared by the following method, which specifically includes the following steps:
[0049] 1. Dissolve 4.8 g of polylactic acid-glycolic acid in 60 mL of hexafluoroisopropanol solvent, and magnetically stir at room temperature for 12 hours to obtain a spinning solution with a polymer concentration of 8% (w / v).
[0050] 2. After the spinning solution was stirred at room temperature overnight, electrospinning was carried out. The stainless steel roller was used as the receiving device, the voltage was 25KV, the receiving distance was 20cm, the feeding rate of the spinning solution was 3.8mL / h, and the spinning time was 9 hours. The obtained thickness was A film of about 200 μm.
[0051] 3. Freeze the obtained fiber membrane at -20°C for 6 hours, and then vacuum-dry it for 72 hours to ensure that the residual solvent is fully volatilized.
[0052] Scanning electron microscope observation is carried out to t
Embodiment 2
[0056] In this embodiment, the haze protective electrospun membrane is prepared by the following method, which specifically includes the following steps:
[0057] 1. Dissolve 4.8 g of polylactic acid-glycolic acid in 40 mL of hexafluoroisopropanol solvent, and magnetically stir at room temperature for 12 hours to obtain a spinning solution with a polymer concentration of 12% (w / v).
[0058] 2. The solution was electrospun, with a stainless steel roller as the receiving device, the voltage was 25KV, the receiving distance was 20cm, the spinning liquid inflow rate was 3.8mL / h, and the spinning was 6h. A film with a thickness of about 200 μm was obtained.
[0059] 3. Freeze the obtained electrospun membrane at -20°C for 6 hours, and then vacuum-dry it for 72 hours to ensure that the residual solvent is fully volatilized.
[0060] Scanning electron microscope observation is carried out to the electrospun filter membrane prepared in embodiment 2, the result is as follows figure
Embodiment 3
[0064] In this embodiment, the haze protective electrospun membrane is prepared by the following method, which specifically includes the following steps:
[0065] 1. Dissolve 4.8 g of polylactic acid-glycolic acid in 30 mL of hexafluoroisopropanol solvent, and magnetically stir at room temperature for 12 hours to obtain a spinning solution with a polymer concentration of 16% (w / v).
[0066] 2. The solution was electrospun, with a stainless steel roller as the receiving device, the voltage was 25KV, the receiving distance was 20cm, the spinning liquid inflow rate was 3.8mL / h, and the spinning was 4.5h. A film with a thickness of about 200 μm was obtained.
[0067] 3. The obtained electrospun membrane was frozen at -20°C for 6 hours, and then vacuum-dried for 72 hours to ensure that the residual solvent was fully volatilized.
[0068] Scanning electron microscope observation is carried out to the electrostatic spinning filter membrane that embodiment 3 prepares, the result is
PUM
Property | Measurement | Unit |
---|---|---|
Diameter | aaaaa | aaaaa |
Diameter | aaaaa | aaaaa |
Maximum tensile strength | aaaaa | aaaaa |
Abstract
Description
Claims
Application Information
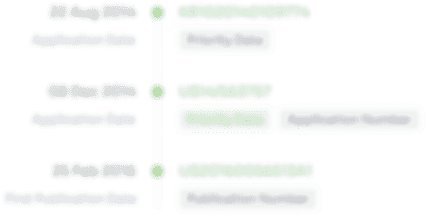
- R&D Engineer
- R&D Manager
- IP Professional
- Industry Leading Data Capabilities
- Powerful AI technology
- Patent DNA Extraction
Browse by: Latest US Patents, China's latest patents, Technical Efficacy Thesaurus, Application Domain, Technology Topic.
© 2024 PatSnap. All rights reserved.Legal|Privacy policy|Modern Slavery Act Transparency Statement|Sitemap