Normal-temperature-curable high-temperature-resistant conveyer belt adhesive and preparation and application method thereof
A room temperature curing and adhesive technology, applied in the direction of bonding method, adhesive type, chloroprene adhesive, etc., can solve the problem of joint strength only reaching 60-70%, short service time, and poor bonding strength Advanced problems, to achieve good benefits, short operating time, good flex resistance
- Summary
- Abstract
- Description
- Claims
- Application Information
AI Technical Summary
Problems solved by technology
Method used
Image
Examples
Embodiment 1
[0023] At first, press chloroprene rubber 70, chlorinated rubber 30, zinc oxide 7, magnesium oxide 5, phenolic resin 20, coupling agent 5, the mass fraction ratio of mixed solvent (toluene, ethyl acetate) 400, these solvents, Put the solid materials into the reaction tank in turn, and stir for 2 hours at 40°C to prepare the adhesive component A;
[0024] Then, when in use, the prepared A component and the B component that is mainly 3,3'-dimethyl-triphenylmethane-4,4',6,6'-tetraisocyanate polymer are divided by 10: The ratio of 1 is mixed evenly, and the adhesive for high temperature resistant conveyor belt can be cured at room temperature;
[0025] Before use, the prepared conveyor belt joints must be polished, cleaned, and dried, and then coated with adhesive, the joints are bonded, and then rolled with a roller or hand hammer, beaten and compacted, cured at room temperature, and the conveyor belt is ready to use .
Embodiment 2
[0027] At first, by chloroprene rubber 70, chlorinated rubber 30, zinc oxide 7, magnesium oxide 5, epoxy ester 20, coupling agent 5, the mass fraction ratio of mixed solvent (toluene, ethyl acetate) 400, these solvents 1. Put the solid materials into the reaction tank in turn, and stir for 1.5 hours at 45°C to obtain the adhesive component A;
[0028] Then, when using the prepared A component and mainly 4,4'-dicarboxy-diphenylmethane-4,4',8,8'-hexaisocyanate polymer B component by 10:1 The proportion of mixing evenly, that is, room temperature curing high temperature resistant conveyor belt adhesive;
[0029] Before use, the prepared conveyor belt joints must be polished, cleaned, and dried, and then coated with adhesive, the joints are bonded, and then rolled with a roller or hand hammer, beaten and compacted, cured at room temperature, and the conveyor belt is ready to use .
Embodiment 3
[0031] At first, press chloroprene rubber 70, chlorinated rubber 30, zinc oxide 7, magnesium oxide 5, ethylene-vinyl acetate copolymer resin 20, coupling agent 5, the mass fraction ratio of mixed solvent (toluene, ethyl acetate) 400, Put these solvents and solid materials into the reaction tank in turn, and stir for 1 hour at 50°C to prepare the adhesive component A;
[0032] Then, when in use, the A component and the B component that is mainly 3,3'-diethyl-triphenylmethane-5,5',8,8'-heptaisocyanate polymer are mixed in a ratio of 10: The ratio of 1 is mixed evenly, and the adhesive for high temperature resistant conveyor belt can be cured at room temperature;
[0033] Before use, the prepared conveyor belt joints must be polished, cleaned, and dried, and then coated with adhesive, the joints are bonded, and then rolled with a roller or hand hammer, beaten and compacted, cured at room temperature, and the conveyor belt is ready to use .
PUM
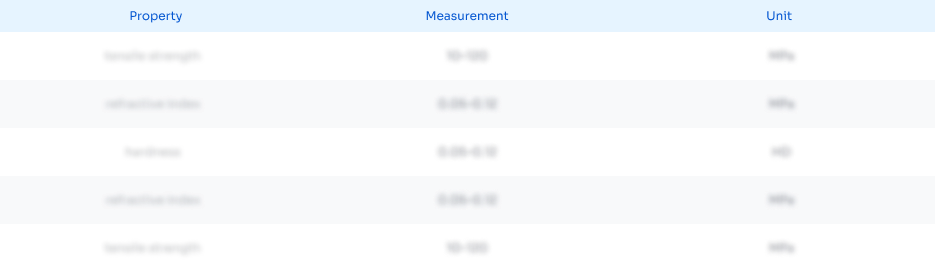
Abstract
Description
Claims
Application Information
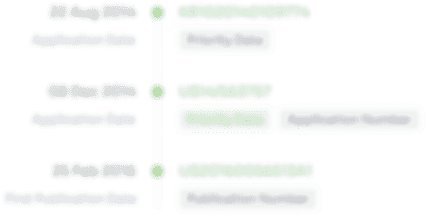
- R&D Engineer
- R&D Manager
- IP Professional
- Industry Leading Data Capabilities
- Powerful AI technology
- Patent DNA Extraction
Browse by: Latest US Patents, China's latest patents, Technical Efficacy Thesaurus, Application Domain, Technology Topic.
© 2024 PatSnap. All rights reserved.Legal|Privacy policy|Modern Slavery Act Transparency Statement|Sitemap