Novel process for precision forging of disc steering knuckle
A technology of steering knuckle and new technology, which is applied to railway car body parts, transportation and packaging, vehicle parts, etc. It can solve the problems of insufficient filling of the head and rod, low production efficiency, unstable quality, etc., and achieve high production efficiency , cost reduction, and the effect of stable forging quality
- Summary
- Abstract
- Description
- Claims
- Application Information
AI Technical Summary
Benefits of technology
Problems solved by technology
Method used
Examples
Embodiment
[0013] 1) Material preparation: use a semi-automatic band sawing machine to saw the Φ150 bar material according to the size Φ150X340±1, and the end face slope is less than 2° to meet the requirements of the upsetting forming process.
[0014] 2) Heating: double-hearth medium-frequency induction furnace heating, heating temperature 1200 ℃, heating cycle 45 seconds, automatic monitoring of blank temperature, automatic discharge, automatic sorting of unqualified temperature blanks, to ensure that the blanks are not overheated or overheated, and the internal quality of the blanks is guaranteed Meet the requirements of forging forming.
[0015] 3) Precision forging: the mold is preheated to 220°C, the mold is lubricated with graphite milk, and the precision forging is formed by the four-station automatic production line of the 8000T hot forging press, and the production cycle is 45 seconds.
[0016] Upsetting: the initial forging temperature is 1180°C, put the heated blank on the upse
PUM
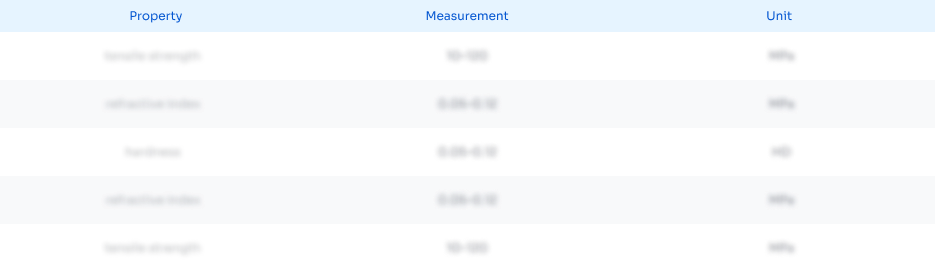
Abstract
Description
Claims
Application Information
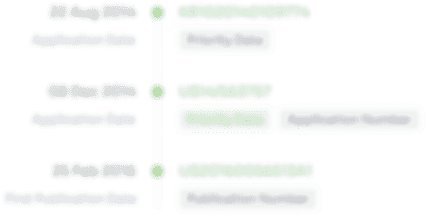
- R&D Engineer
- R&D Manager
- IP Professional
- Industry Leading Data Capabilities
- Powerful AI technology
- Patent DNA Extraction
Browse by: Latest US Patents, China's latest patents, Technical Efficacy Thesaurus, Application Domain, Technology Topic.
© 2024 PatSnap. All rights reserved.Legal|Privacy policy|Modern Slavery Act Transparency Statement|Sitemap