Autoclaved/steam cured brick prepared from industrial waste and preparation process thereof
A technology for industrial waste and preparation process, applied in the field of industrial waste recycling, can solve the problems of complex compound activator formula, complex additive types, and large use limitations, and achieves excellent performance, short production cycle, and economical Effect of processing fees
- Summary
- Abstract
- Description
- Claims
- Application Information
AI Technical Summary
Problems solved by technology
Method used
Examples
Example Embodiment
[0028] Example 1
[0029] An autoclaved / steam-cured brick prepared from industrial waste, the weight ratio of the raw materials used is as follows:
[0030] Waste cement slurry 15%, slag 35%, medium sand 30%, crushed stone 20%,
[0031] The waste cement slurry and slag are collected from the pipe pile production workshop and the boiler room and transported to the steam-cured brick production workshop. The waste cement slurry is the waste liquid thrown out during the high-speed centrifugal molding process when the prestressed concrete pipe pile is produced, and the slag is coal. Combustion solid residue, slag after drying treatment, crushed to a particle diameter of 1-5mm, add 0.2wt% of activator, the activator is sodium silicate, sodium sulfate and calcium formate mixed in a weight ratio of 1:1:0.5.
[0032] Medium sand is sand with a fineness modulus of 2.3-3.0;
[0033] The maximum particle size of the crushed stone is not more than 10mm.
[0034] The preparation process of autoclaved
Example Embodiment
[0038] Example 2
[0039] An autoclaved / steam-cured brick prepared from industrial waste is characterized by the weight ratio of raw materials used as follows:
[0040] 25% waste cement slurry, 60% slag, 10% medium sand, 5% crushed stone,
[0041] The waste cement slurry and slag are collected from the pipe pile production workshop and the boiler room and transported to the steam-cured brick production workshop. After drying, the slag is crushed to a particle diameter of 1-5mm. Medium sand is used for sand and crushed stone is used for gravel. The maximum particle size of the crushed stone is not more than 15mm. Among them, the waste cement slurry is the waste liquid thrown out during the high-speed centrifugal molding process in the production of prestressed concrete pipe piles; the slag is the solid residue from coal combustion, with a particle size of 1-5 mm, which contains 0.5wt% of activator, activator It is obtained by mixing sodium silicate, sodium sulfate and calcium formate
PUM
Property | Measurement | Unit |
---|---|---|
Maximum particle size | aaaaa | aaaaa |
Particle size | aaaaa | aaaaa |
Particle size | aaaaa | aaaaa |
Abstract
Description
Claims
Application Information
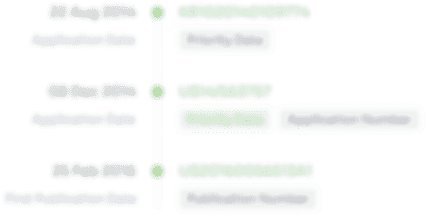
- R&D Engineer
- R&D Manager
- IP Professional
- Industry Leading Data Capabilities
- Powerful AI technology
- Patent DNA Extraction
Browse by: Latest US Patents, China's latest patents, Technical Efficacy Thesaurus, Application Domain, Technology Topic.
© 2024 PatSnap. All rights reserved.Legal|Privacy policy|Modern Slavery Act Transparency Statement|Sitemap