Alkali-resistant anticorrosive paint
An anti-corrosion coating and alkali-resistant technology, applied in anti-corrosion coatings, coatings, etc., can solve problems such as poor erosion resistance, short anti-corrosion period, unstable paint film, etc., and achieve strong corrosion resistance, enhanced quality, and metal adhesion Good results
- Summary
- Abstract
- Description
- Claims
- Application Information
AI Technical Summary
Benefits of technology
Problems solved by technology
Method used
Examples
Embodiment 1
[0028] An alkali-resistant anticorrosion coating, it is made up of two components of A and B, and described A component is made up of the raw material of following weight portion (kg):
[0029] Epoxy resin E44 74, high chlorinated polyethylene resin ((chlorine content 65%-M)) 25, mica powder 16, titanium dioxide 6, sodium carboxymethyl cellulose 7, dimethyl terephthalate 6, propane Triol 6, ethyl acrylate 2-4, tung oil 3, polyacrylamide 3, diethylamine 3, acetyl triethyl citrate 3, ammonium dihydrogen phosphate 4, sodium molybdate 5, 2,6-di-tert-butyl 4 p-cresol, 12 composite modifiers, 30 xylene, 10 n-butanol, 0.8 anilinomethyltriethoxysilane, 0.5 dimethyl silicone oil;
[0030] Described composite modifier is made up of the following raw materials of weight part:
[0031] 35-40 Baume degree water glass 50, aluminum sulfate 100, nano silicon dioxide particles 45, sorbitan monooleate 2, polyoxyethylene ether 2, carboxymethyl cellulose sodium 1, dodecylbenzene Sodium sulfonate 4
PUM
Property | Measurement | Unit |
---|---|---|
Flexibility | aaaaa | aaaaa |
Adhesion | aaaaa | aaaaa |
Abstract
Description
Claims
Application Information
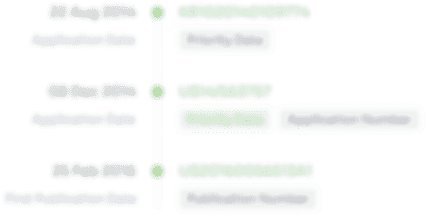
- R&D Engineer
- R&D Manager
- IP Professional
- Industry Leading Data Capabilities
- Powerful AI technology
- Patent DNA Extraction
Browse by: Latest US Patents, China's latest patents, Technical Efficacy Thesaurus, Application Domain, Technology Topic.
© 2024 PatSnap. All rights reserved.Legal|Privacy policy|Modern Slavery Act Transparency Statement|Sitemap