Manufacturing method of steel ratchet wheel
A ratchet and steel technology, which is applied to mechanical equipment, components with teeth, belts/chains/gears, etc., can solve the problems of easy generation of transition scale, large labor costs, large material loss, etc., and achieve mechanical properties Improve, save product materials, improve the effect of mold life
- Summary
- Abstract
- Description
- Claims
- Application Information
AI Technical Summary
Problems solved by technology
Method used
Examples
Example Embodiment
[0027] A method for preparing a steel ratchet includes the following steps:
[0028] a. Steps of pouring Φ120×47mm rod-shaped blanks
[0029] The weight percentage of chemical composition in the rod-shaped blank is: C 0.24-0.40%, Mn 1.2-2.0%, Si 0.7-1.3, Cr 0.4-1.2%, W 0.42-0.8%, M0 0.4-0.8%, Al 0.04-0.2%, Cu 0.22~0.52%, P≤0.033%, S≤0.035%, the remainder is Fe and unavoidable impurities; the temperature of the casted rod-shaped billet is reduced to 340℃, and then heated to 700-750℃, heat preservation 3-5 After hours, the furnace is cooled to 250°C, holding for 4-5 hours, then heating to 600-650°C, holding for 5-6 hours, cooling to 400°C at 45°C / hour, and then cooling to 140°C at 25°C / hour;
[0030] b. Machining steps
[0031] 1. Rough turning, rough turning of inner hole to Φ60mm, 0.5mm margin for other dimensions, and inner hole chamfering Φ80mm×120°;
[0032] 2. Fine turning, the inner hole is fine turning and the outer circle is bright, and the other dimensions are finely turned i
PUM
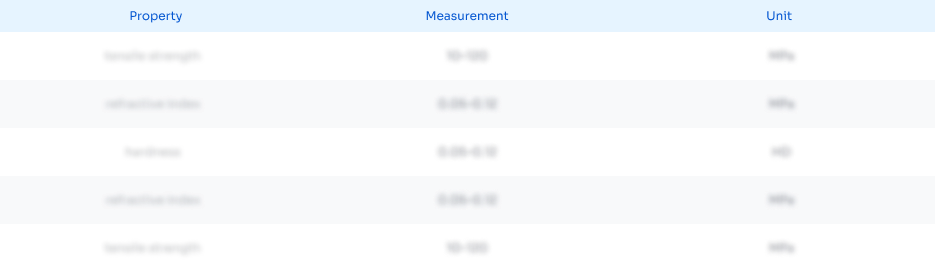
Abstract
Description
Claims
Application Information
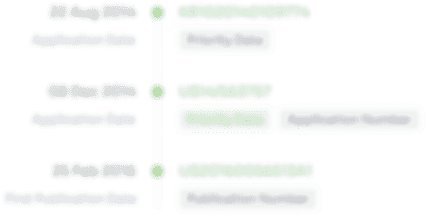
- R&D Engineer
- R&D Manager
- IP Professional
- Industry Leading Data Capabilities
- Powerful AI technology
- Patent DNA Extraction
Browse by: Latest US Patents, China's latest patents, Technical Efficacy Thesaurus, Application Domain, Technology Topic.
© 2024 PatSnap. All rights reserved.Legal|Privacy policy|Modern Slavery Act Transparency Statement|Sitemap