Machine tool cutting force simulation loading device
A loading device and cutting force technology, applied in the direction of metal processing equipment, metal processing machinery parts, measuring/indicating equipment, etc., can solve the problems of complex structure and small load, and achieve wide applicability, wide load range and simple structure Effect
- Summary
- Abstract
- Description
- Claims
- Application Information
AI Technical Summary
Benefits of technology
Problems solved by technology
Method used
Image
Examples
Embodiment Construction
[0012] The present invention will be further described below in conjunction with accompanying drawing:
[0013] Depend on Figure 1 to Figure 3 As shown, a cutting force simulation loading device for a machine tool includes a loading mandrel 4. During the experiment, the loading mandrel 4 drives the entire loading device 3 to be connected to the main shaft 2 in the headstock 1. A platform 5 is provided at the bottom of the loading device 3. A servo motor 6 is fixed on the platform 5 through a motor support 7 . The right end of the loading mandrel 4 is placed in the main support 10, and the outside of the loading mandrel 4 is connected with a radial bearing sleeve 15 through a rolling bearing B18, and the outside of the radial bearing sleeve 15 is provided with a rotating body 16. There is a groove, and a radial hydraulic cylinder 11 is built in the groove, and the piston rod of the radial hydraulic cylinder 11 abuts on the outer surface of the radial bearing sleeve 15 . The rot
PUM
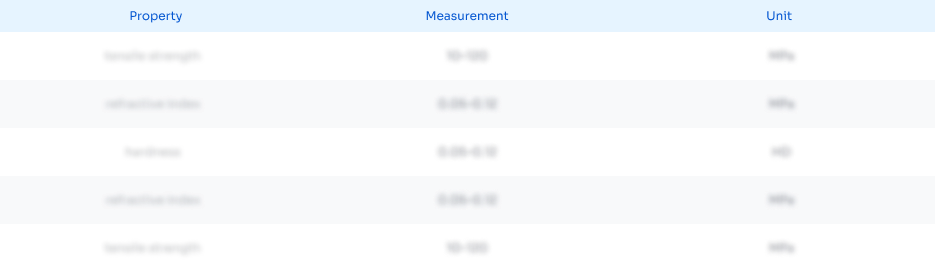
Abstract
Description
Claims
Application Information
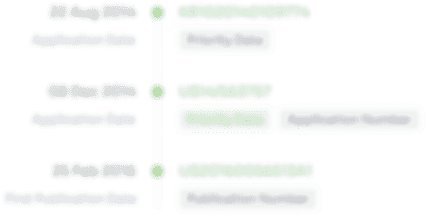
- R&D Engineer
- R&D Manager
- IP Professional
- Industry Leading Data Capabilities
- Powerful AI technology
- Patent DNA Extraction
Browse by: Latest US Patents, China's latest patents, Technical Efficacy Thesaurus, Application Domain, Technology Topic.
© 2024 PatSnap. All rights reserved.Legal|Privacy policy|Modern Slavery Act Transparency Statement|Sitemap