Processing equipment and manufacturing method of hollow train shaft
一种加工设备、火车轴的技术,应用在金属加工设备、制造工具、金属轧制等方向,能够解决降低零件承载能力、生产效率低、加工余量大等问题,达到节约材料、提高生产效率的效果
- Summary
- Abstract
- Description
- Claims
- Application Information
AI Technical Summary
Problems solved by technology
Method used
Examples
Embodiment
[0028] Example A processing and manufacturing equipment for hollow train axles
[0029] figure 1 The overall structure of the processing and manufacturing equipment for the hollow train axle of this embodiment is shown, which is mainly composed of the feeding system 、 Pushing device 6, cross wedge rolling mill 1, and mandrel rod advancing and retreating mechanism are composed, and the above-mentioned parts are arranged in a straight line.
[0030] The feeding system is a transmission mechanism that transfers the heated hollow bar from the heating furnace to the feeding platform, and is mainly composed of a power system and a transmission chain plate.
[0031] The pushing device is mainly composed of an air source, a cylinder, a pushing head 7, and a feed table 8, and the pushing head 7 is connected to the cylinder.
[0032] The cross wedge rolling mill is mainly composed of a motor, a reducer, a sub-gearbox, a rolling mill archway, and a rolling mandrel. The connection...
PUM
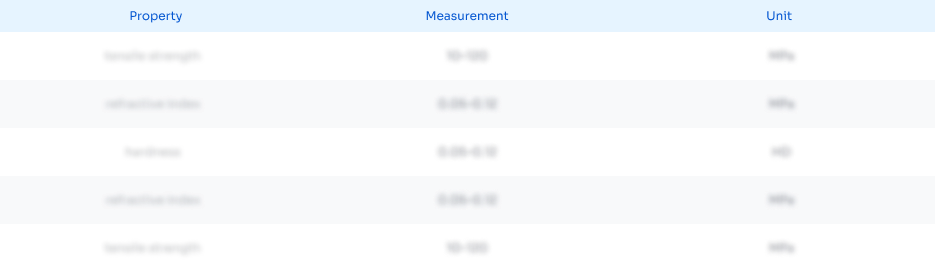
Abstract
Description
Claims
Application Information
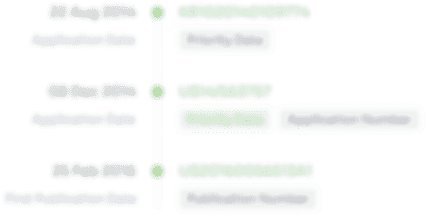
- R&D Engineer
- R&D Manager
- IP Professional
- Industry Leading Data Capabilities
- Powerful AI technology
- Patent DNA Extraction
Browse by: Latest US Patents, China's latest patents, Technical Efficacy Thesaurus, Application Domain, Technology Topic.
© 2024 PatSnap. All rights reserved.Legal|Privacy policy|Modern Slavery Act Transparency Statement|Sitemap