Novel rubber good in oil resistance and preparation method thereof
A high-performance and good technology, applied in the field of rubber materials, can solve problems such as hindering application, and achieve the effect of broadening the scope of application
- Summary
- Abstract
- Description
- Claims
- Application Information
AI Technical Summary
Benefits of technology
Problems solved by technology
Method used
Examples
Embodiment 1
[0027] (1) Add 15 parts of chlorinated ethylene-propylene rubber, 20 parts of nitrile rubber, and 25 parts of fluororubber into the internal mixer to masticate evenly;
[0028] (2) Continue to add 3 parts of zinc oxide, 5 parts of calcium borate, 3 parts of magnesium dimethacrylate, 10 parts of white carbon black, 20 parts of paraffin, bismaleyl 12 parts of amine resin, 15 parts of phenol-urea-formaldehyde co-condensation resin, 2 parts of 2-(p-chlorobenzylthio)benzimidazole, 15 parts of anti-aging agent are mixed; the speed of the mixing process is 55rpm, and the mixing The mixing time is 5 minutes, the mixing temperature is 65°C, and the mixing heating rate is 1.5°C / min; until the mixing is uniform, the sheet is produced to obtain the mixing mixture;
[0029] (3) Vulcanize the kneading mixture described in step (2), the vulcanization time is 30min, the vulcanization temperature is 150°C, and the vulcanization pressure is 8MPa; after taking it out, it is dried at 100°C for 60m
Embodiment 2
[0031] (1) Add 35 parts of chlorinated ethylene-propylene rubber, 30 parts of nitrile rubber, and 40 parts of fluororubber into the internal mixer to masticate evenly;
[0032] (2) Continue to add 7 parts of zinc oxide, 10 parts of calcium borate, 8 parts of magnesium dimethacrylate, 15 parts of white carbon black, 40 parts of paraffin, bismaleyl 20 parts of amine resin, 28 parts of phenol-urea-formaldehyde co-condensation resin, 7 parts of 2-(p-chlorobenzylthio)benzimidazole, 22 parts of anti-aging agent are mixed; the speed of the mixing process is 65rpm, and the mixing The mixing time is 8 minutes, the mixing temperature is 75°C, and the mixing heating rate is 2.5°C / min; until the mixing is uniform, the sheet is produced to obtain the mixing mixture;
[0033] (3) Vulcanize the kneading mixture described in step (2), the vulcanization time is 45min, the vulcanization temperature is 170°C, and the vulcanization pressure is 15MPa; after taking it out, it is dried at 100°C for 6
Embodiment 3
[0035] (1) Add 20 parts of chlorinated ethylene-propylene rubber, 25 parts of nitrile rubber, and 30 parts of fluororubber into the internal mixer to masticate evenly;
[0036] (2) Continue to add 5 parts of zinc oxide, 5.5 parts of calcium borate, 4 parts of magnesium dimethacrylate, 12 parts of white carbon black, 28 parts of paraffin, bismaleyl 15 parts of amine resin, 22 parts of phenol-urea-formaldehyde co-condensation resin, 3.5 parts of 2-(p-chlorobenzylthio)benzimidazole, 18 parts of anti-aging agent are mixed; the speed of the mixing process is 60rpm, and the mixing The mixing time is 6 minutes, the mixing temperature is 70°C, and the mixing heating rate is 2°C / min; until the mixing is uniform, the sheet is produced to obtain the mixing mixture;
[0037] (3) Vulcanize the kneading mixture described in step (2), the vulcanization time is 40min, the vulcanization temperature is 165°C, and the vulcanization pressure is 12MPa; after taking it out, it is dried at 100°C for
PUM
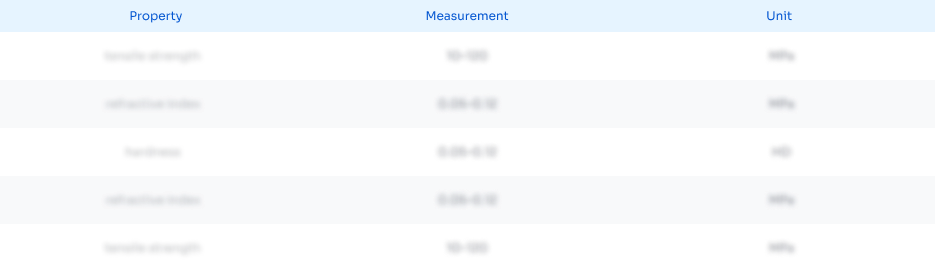
Abstract
Description
Claims
Application Information
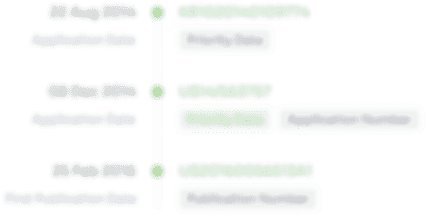
- R&D Engineer
- R&D Manager
- IP Professional
- Industry Leading Data Capabilities
- Powerful AI technology
- Patent DNA Extraction
Browse by: Latest US Patents, China's latest patents, Technical Efficacy Thesaurus, Application Domain, Technology Topic.
© 2024 PatSnap. All rights reserved.Legal|Privacy policy|Modern Slavery Act Transparency Statement|Sitemap