Polymerization device in production process of polyethylene oxide products
A technology of polyethylene oxide and polymerization equipment, which is applied in the direction of chemical/physical/physical chemical fixed reactors, etc., can solve the problems of polymerization equipment amplification, unevenness, implosion particle size and molecular weight, etc., and achieve the effect of avoiding local implosion
- Summary
- Abstract
- Description
- Claims
- Application Information
AI Technical Summary
Problems solved by technology
Method used
Image
Examples
Embodiment 1
[0017] Example 1 (Production of 100,000 molecular weight products):
[0018] 1. After the speed of the stirring device 2 in the main body 1 of the polymerizer is set to 130 revolutions per minute, open the solvent feed valve on the solvent inlet 6-2, and drive 3m into the main body 1 of the polymerizer 3 Solvent, when the liquid level of the main body 1 of the polymerizer reaches 3m 3 When, close the solvent feed valve.
[0019] 2. Turn on the catalyst feeding device 3, and add the metered catalyst into the main body 1 of the polymerization vessel through the catalyst inlet 6-1; at the same time, turn on the shear 4.
[0020] 3. Open the cooling device 5 on the main body 1 of the polymerizer, make the cooling water circulate through the chilled water inlet 18 and chilled water outlet 13 on the cooling pipe 21, and turn on the ethylene oxide feed on the ethylene oxide inlet 6-3 The valve is used to feed ethylene oxide into the main body 1 of the polymerizer. During the reaction, the rea
Embodiment 2
[0023] Example 2 (Production of 3 million molecular weight products):
[0024] 1. After the rotation speed of the stirring device 2 in the main body 1 of the polymerizer is set to 90 rpm, open the solvent feed valve on the solvent inlet 6-2, and drive 3m into the main body 1 of the polymerizer 3 Solvent, when the liquid level in the main body 1 of the polymerizer reaches 3m 3 When, close the solvent feed valve.
[0025] 2. Turn on the catalyst feeding device 3, and add the metered catalyst into the main body 1 of the polymerization vessel through the catalyst inlet 6-1; at the same time, turn on the shear 4.
[0026] 3. Open the cooling device 5 on the main body 1 of the polymerizer, make the cooling water circulate through the chilled water inlet 18 and chilled water outlet 13 on the cooling pipe 21, and turn on the ethylene oxide feed on the ethylene oxide inlet 6-3 Valve to pass ethylene oxide into the polymerization vessel. During the reaction process, the reaction temperature is
Embodiment 3
[0029] Example 3 (Production of 8 million molecular weight products):
[0030] 1. After setting the stirring speed of the polymerization kettle to 50 rpm, open the solvent feed valve and drive 2.5m into the polymerization kettle 3 Solvent, when the liquid level in the kettle reaches 2.5m 3 When, close the solvent feed valve.
[0031] 2. Turn on the catalyst feeding device 3, and add the metered catalyst into the main body 1 of the polymerization vessel through the catalyst inlet 6-1; at the same time, turn on the shear 4.
[0032] 3. Open the cooling device 5 on the main body 1 of the polymerizer, make the cooling water circulate through the chilled water inlet 18 and chilled water outlet 13 on the cooling pipe 21, and turn on the ethylene oxide feed on the ethylene oxide inlet 6-3 Valve to pass ethylene oxide into the polymerization vessel. During the reaction process, the reaction temperature is controlled to be 30-55°C, the pressure is controlled to be 0.3-0.6 MPa, the feeding amoun
PUM
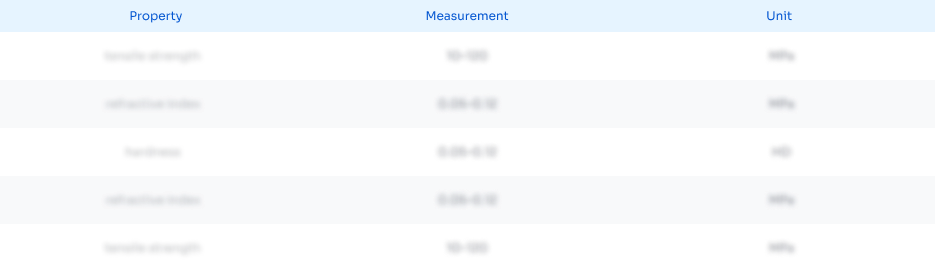
Abstract
Description
Claims
Application Information
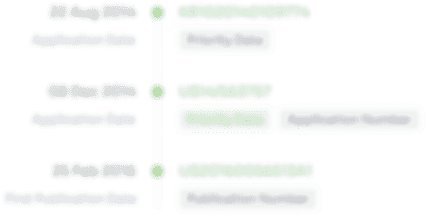
- R&D Engineer
- R&D Manager
- IP Professional
- Industry Leading Data Capabilities
- Powerful AI technology
- Patent DNA Extraction
Browse by: Latest US Patents, China's latest patents, Technical Efficacy Thesaurus, Application Domain, Technology Topic.
© 2024 PatSnap. All rights reserved.Legal|Privacy policy|Modern Slavery Act Transparency Statement|Sitemap