High-temperature-resistant high-performance rare earth permanent magnet material
A rare earth permanent magnet, high-performance technology, applied in the field of alloys, to achieve the effect of expanding the scope of application, high temperature resistance and high stability
- Summary
- Abstract
- Description
- Claims
- Application Information
AI Technical Summary
Benefits of technology
Problems solved by technology
Method used
Examples
Embodiment 1
[0024] A high-temperature resistant high-performance rare earth permanent magnet material, including rare earth elements, iron, boron, molybdenum, silicon, vanadium, calcium, zirconium, chromium, nickel, the weight percentage of each component is: boron 1.0%, molybdenum 0.1%, silicon 3%, vanadium 1.5%, calcium 0.3%, zirconium 0.1%, chromium 0.2%, nickel 3%, neodymium 20%, holmium 0.5%, dysprosium 2%, praseodymium 1.5%, the balance is iron and unavoidable impurities;
[0025] Specific steps include:
[0026] (1) Raw material preparation: mix the surface-cleared raw materials according to the weight ratio;
[0027] (2) Ingot casting: Put the raw materials into the melting furnace, vacuumize, melt and cast into ingots under the protection of 0.05MPa argon, and then place the ingots in a vacuum furnace for homogenization treatment. The temperature of the treatment is 950°C for 9 hours;
[0028] (3) Powder making: hydrogen crushing the homogenized ingot to 200μm alloy powder, and th
Embodiment 2
[0034] A high-temperature resistant high-performance rare earth permanent magnet material, including rare earth elements, iron, boron, molybdenum, silicon, vanadium, calcium, zirconium, chromium, nickel, the weight percentage of each component is: boron 1.2%, molybdenum 0.14%, silicon 2%, vanadium 2%, calcium 0.15%, zirconium 0.3%, chromium 0.4%, nickel 2%, neodymium 24%, holmium 0.6%, dysprosium 2.4%, praseodymium 1.8%, the balance is iron and unavoidable impurities;
[0035] Specific steps include:
[0036] (1) Raw material preparation: mix the surface-cleared raw materials according to the weight ratio;
[0037] (2) Ingot casting: Put the raw materials into the melting furnace, vacuumize, melt and cast into ingots under the protection of 0.05MPa argon, and then place the ingots in a vacuum furnace for homogenization treatment. The temperature of the treatment is 900°C for 10 hours;
[0038] (3) Milling: Hydrogen crushing of the homogenized ingot to 230μm alloy powder, follow
Embodiment 3
[0044] A high-temperature resistant high-performance rare earth permanent magnet material, including rare earth elements, iron, boron, molybdenum, silicon, vanadium, calcium, zirconium, chromium, nickel, the weight percentage of each component is: boron 1.4%, molybdenum 0.06%, silicon 1%, vanadium 2.5%, calcium 0.45%, zirconium 0.4%, chromium 0.1%, nickel 4.5%, neodymium 28%, holmium 0.7%, dysprosium 2.8%, praseodymium 2.1%, the balance is iron and unavoidable impurities;
[0045] Specific steps include:
[0046] (1) Raw material preparation: mix the surface-cleared raw materials according to the weight ratio;
[0047] (2) Ingot casting: Put the raw materials into the melting furnace, vacuumize, melt and cast into ingots under the protection of 0.05MPa argon, and then place the ingots in a vacuum furnace for homogenization treatment. The temperature of the treatment is 960°C for 9 hours;
[0048] (3) Powder making: hydrogen crushing the homogenized ingot to 250μm alloy powder, an
PUM
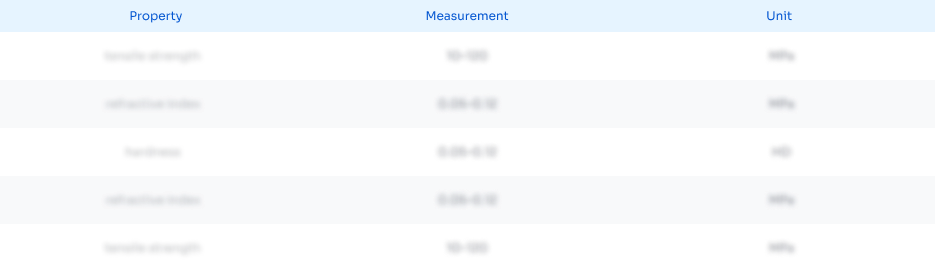
Abstract
Description
Claims
Application Information
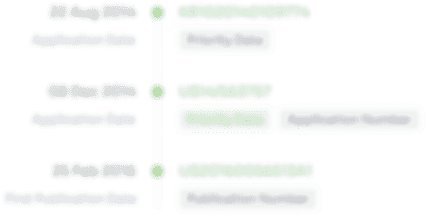
- R&D Engineer
- R&D Manager
- IP Professional
- Industry Leading Data Capabilities
- Powerful AI technology
- Patent DNA Extraction
Browse by: Latest US Patents, China's latest patents, Technical Efficacy Thesaurus, Application Domain, Technology Topic.
© 2024 PatSnap. All rights reserved.Legal|Privacy policy|Modern Slavery Act Transparency Statement|Sitemap